3.15. Input and Output¶
3.15.1. Input Description¶
The input variables used in the pre-voiding subassembly thermal hydraulics calculations are listed in Table 3.14.1. Some additional comments on some of these input variables are listed below.
3.15.1.1. Per Pin Basis¶
All of the core channel thermal hydraulic input to SAS4A/SASSYS‑1 is on a per pin basis rather than a per subassembly basis. Thus, the initial flow rate, W0, is kg/s per pin; and the perimeters SRFSTZ and SER are perimeters per pin. Also, ACCZ is a coolant flow area per pin, and the variables DZIAB and DZIAT are ratios of inertial lengths to flow areas per pin.
3.15.1.2. Structure/Duct Wall and Wrapper Wires¶
Typically a SAS4A/SASSYS‑1 channel represents an average pin in a subassembly. In this case, the structure normally represents one pin’s share of the duct wall, and it may also include the wrapper wire. If there are N pins in the subassembly, then the thickness used for the structure is the actual duct wall thickness, and the perimeter used for the structure is the duct wall perimeter divided by N. The wrapper wire can be either lumped with the cladding or included in the structure. Since wrapper wires are in much better contact with the cladding than with the duct wall, the most accurate treatment of the wrapper wire is probably to lump it with the cladding by increasing the specific heat of the cladding by enough to account for the total heat capacity of the cladding plus the wrapper wire. The cladding dimensions would not be changed.
The problem with lumping the wrapper wires with the duct wall to produce a single “structure” is that typically the duct wall has a much larger ratio of volume to wetted surface area than a wrapper wire, so the wrapper wire temperature will respond much more rapidly than the duct wall temperature to a change in coolant temperature. The heat capacity of the duct wall is considerably greater than the heat capacity of all of the wrapper wires in a subassembly, but the total perimeter of the wrapper wires is greater than the perimeter of the duct wall. If the duct wall and wrapper wires are lumped together, then the thickness of the structure should be determined by the thickness of the duct wall, since the duct wall contains most of the heat capacity. Then the perimeter of the structure should be chosen to conserve the total volume or total heat capacity of the duct wall plus wrapper wires.
A SAS4A/SASSYS‑1 channel can be used to represent a central pin rather than an average pin in a subassembly. In this case, the duct wall would probably be ignored, and the “structure: would represent only the wrapper wire. The perimeter of the structure would equal the perimeter of a wrapper wire, and the thickness of the structure would equal one half of the wrapper wire radius in order to conserve volume.
Variable |
Reference Eq. No. |
Input Variable |
Input Block |
Location Number |
Suggested Value |
External Reference |
---|---|---|---|---|---|---|
NCHAN |
1 |
1 |
1-34 |
|||
IFUEL1 |
1 |
3 |
1-8 |
|||
ICLAD1 |
1 |
4 |
1-3 |
|||
ITKEL |
1 |
7 |
0 or 1 |
|||
IPOWOP |
1 |
9 |
1 |
|||
MAXSTP |
1 |
11 |
– |
|||
IPO |
1 |
12 |
20-50 |
|||
IPOBOI |
1 |
13 |
20-50 |
|||
IBLPRT |
1 |
14 |
0 |
|||
INAS3D |
1 |
29 |
0 |
|||
ISSNUL |
1 |
87 |
– |
|||
IPRSNL |
1 |
88 |
||||
EPSTEM |
11 |
1 |
.1 or less |
|||
DTMXB |
11 |
6 |
.01 |
|||
DTFUEL |
11 |
10 |
50 |
|||
DTCLAD |
11 |
11 |
30 |
|||
POW |
12 |
1 |
||||
ρ |
3.3.1 |
COEFDS(1) |
13 |
1 |
11080 |
|
COEFDS(2) |
13 |
2 |
2.04x10-5 |
|||
COEFDS(3) |
13 |
3 |
8.70x10-9 |
|||
k |
3.3.1 |
COEFK |
13 |
4 |
||
k |
3.3.1 |
EXKTB |
13 |
11 |
||
EXKTM |
13 |
71 |
||||
ρ |
3.3.1 |
RHOTAB |
13 |
91 |
||
RHOTEM |
13 |
251 |
||||
k |
3.3.1 |
XKTAB |
13 |
420 |
||
XKTEM |
13 |
580 |
||||
\({\overline{c}}_{\text{f}}\) |
3.3-16 |
CPFTAB |
13 |
606 |
||
CPFTEM |
13 |
766 |
||||
Tsol |
3.3-92 |
TFSOL |
13 |
786 |
||
Tliq |
3.3-93 |
TFLIQ |
13 |
794 |
||
Umelt |
3.3-3 |
UFMELT |
13 |
802 |
||
Umelt |
3.3-3 |
UEMELT |
13 |
816 |
||
ce |
3.3-32 |
CPCTAB |
13 |
819 |
||
ρece |
COCTEM |
13 |
879 |
|||
CROETB |
13 |
990 |
||||
CROETM |
13 |
1050 |
||||
px |
3.12-1 |
PX |
14 |
1 |
||
Tin |
3.3-101 |
TOTAB |
14 |
45 |
||
TOTME |
14 |
65 |
||||
\(z_{\text{pll}}\) |
3.9-30 |
ZPLENL |
14 |
87 |
||
\(z_{\text{plu}}\) |
3.9-27 |
ZPLENU |
14 |
88 |
||
Mmix |
3.3-99 |
XMXMSI |
14 |
93 |
||
Mmix |
3.3-99 |
XMXMS0 |
14 |
94 |
||
τmix |
3.3-101 |
TIMMIX |
14 |
95 |
||
IRHOK |
51 |
3 |
||||
NPLN |
51 |
4 |
2-6 |
|||
NREFB |
51 |
5 |
1-5 |
|||
NREFT |
51 |
6 |
1-5 |
|||
NZNODE |
51 |
7 |
||||
NT |
NT |
51 |
14 |
4-11 |
||
IFUELV |
51 |
15 |
1-IFUEL1 |
|||
IFUELB |
51 |
16 |
1-IFUEL1 |
|||
ICLADV |
51 |
17 |
1-ICLAD1 |
|||
NGRDSP |
51 |
18 |
0-10 |
|||
IHGAP |
51 |
24 |
0 or 1 |
|||
NPIN |
51 |
25 |
1 or more |
|||
NSUBAS |
51 |
26 |
1 or more |
|||
MZUB |
51 |
27 |
0-24 |
|||
MZLB |
51 |
28 |
0-24 |
|||
ILAG |
51 |
34 |
0 |
|||
IEQMAS |
51 |
118 |
0 |
|||
IFRFAC |
51 |
186 |
||||
NCHCH |
51 |
205 |
||||
ICHCH |
51 |
206 |
||||
JJMLTP |
51 |
214 |
||||
IAXCON |
51 |
284 |
||||
Ac |
3.3-5 |
ACCZ |
61 |
1 |
>0 |
|
Δz |
3.3-6 |
AXHI |
61 |
8 |
>0 |
|
Dh |
3.3-9 |
DHZ |
61 |
32 |
>0 |
|
dsti |
3.3-45 |
DSTIZ |
61 |
39 |
>0 |
|
dsto |
3.3-47 |
DSTOZ |
61 |
46 |
>0 |
|
PLENL |
61 |
53 |
>0 |
|||
RBR |
61 |
54 |
>ROUTFP |
|||
RER |
61 |
78 |
>RBR |
|||
rbrp |
3.3-68 |
RBRPL |
61 |
102 |
>0 |
|
rcrp |
3.3-73 |
RERPL |
61 |
103 |
>RBRPL |
|
RINFP |
61 |
104 |
||||
ROUTFP |
61 |
128 |
>RINFP |
|||
ZONEL |
61 |
152 |
>0 |
|||
Spt |
3.3-40 |
SRFSTZ |
61 |
159 |
||
AREAPC |
61 |
166 |
>0 |
|||
dro |
3.3-59 |
DRFO |
61 |
169 |
>0 |
|
RBRO |
61 |
180 |
>0 |
|||
RERO |
61 |
181 |
>0 |
|||
Scr |
3.3-62 |
SER |
61 |
182 |
>0 |
|
dri |
3.3-56 |
DRFI |
61 |
189 |
>0 |
|
NPI |
3.11-1 |
XXNPIN |
61 |
274 |
>0 |
|
γs |
3.3-22 |
GAMSS |
62 |
2 |
||
γc |
3.3-6 |
GAMTNC |
62 |
4 |
||
γe |
3.3-23 |
GAMTNE |
62 |
5 |
||
PSHAPE |
62 |
6 |
||||
Pr |
3.3-22 |
PSHAPR |
62 |
30 |
||
AHBPAR |
63 |
2 |
||||
BHBPAR |
63 |
3 |
||||
CHIBPAR |
63 |
4 |
||||
HBMAX |
63 |
5 |
||||
HBMIN |
63 |
6 |
||||
HBPAR |
63 |
7 |
||||
ksi |
3.3-43 |
XKSTIZ |
63 |
11 |
||
kso |
3.3-46 |
XKSTOZ |
63 |
18 |
||
εσ |
3.3-4 |
DEL |
63 |
25 |
||
kr |
3.3-57 |
XKRF |
63 |
28 |
||
(ρc)sti |
3.3-45 |
RHOCSI |
63 |
37 |
>0 |
|
(ρc)sto |
3.3-47 |
RHOCSO |
63 |
44 |
>0 |
|
(ρc)r |
3.3-56 |
RHOCR |
63 |
51 |
>0 |
|
(ρc)g |
3.3-68 |
RHOCG |
63 |
58 |
>0 |
|
Rg |
3.3-71 |
RG |
63 |
59 |
>0 |
|
αf |
3.10-4 |
FUELEX |
63 |
73 |
||
αe |
3.10-5 |
CLADEX |
63 |
74 |
||
Yf |
3.10-8 |
YFUEL |
63 |
75 |
||
Ye |
3.10-9 |
YCLAD |
63 |
76 |
||
FULREX |
63 |
77 |
||||
CLDREX |
63 |
78 |
||||
\((\text{HA}_{\text{I,M}}\) |
3.11-1 |
HACHCH |
63 |
82 |
||
1/γht |
3.3-116 |
TAVINV |
63 |
104 |
.5-5 |
|
Afr |
3.8-3 |
AFR |
64 |
1 |
.1875 |
|
bfr |
3.8-3 |
BFR |
64 |
2 |
-.2 |
|
c1 |
3.3-9 |
C1 |
64 |
3 |
.025 |
2-5 |
c2 |
3.3-9 |
C2 |
64 |
4 |
.8 |
2-5 |
c3 |
3.3-9 |
C3 |
64 |
5 |
4.8 |
2-5 |
DWMAX |
64 |
6 |
.2 |
|||
ReL |
3.9-3 |
RELAM |
64 |
7 |
2100 |
|
AfL |
3.9-3 |
AFLAM |
64 |
8 |
64 |
|
W0 |
64 |
47 |
||||
Kor |
3.9-12 |
XKORV |
64 |
48 |
||
XKORGD |
64 |
64 |
||||
\(\left(\frac{\Delta z_i}{A}\right)_{b}\) |
3.9-6 |
DZIAB |
64 |
65 |
>0 |
|
\(\left(\frac{\Delta z_i}{A}\right)_{f}\) |
3.9-6 |
DZIAT |
64 |
66 |
||
Tout |
3.3.-100 |
DTLMAX |
64 |
69 |
15 |
|
U1 |
3.10-1 |
TUPL |
64 |
74 |
||
U2 |
3.10-2 |
UACH1 |
64 |
189 |
||
UACH2 |
64 |
190 |
3.15.1.3. Empty Reflector Region¶
Sometimes a reflector zone is used to represent an empty section of a subassembly. The duct wall is usually represented by the structure; and since there is nothing but sodium inside the duct wall, there is nothing for the reflector to represent. The code requires a “reflector” in every axial zone except the pin section, so some input for the reflector must be included. The reflector perimeter, SER, cannot be zero; but it can be set to a very small value, such as \(10^{-9}\), so that it would have no impact on coolant temperatures. Also, the total reflector thickness, DRFI plus DRFO, must be a reasonable value, 0.003 m or more, to prevent numerical instabilities in the reflector temperature calculations in the boiling module. The pre-voiding reflector temperature calculations are numerically stable for any reflector greater than zero.
3.15.1.4. Structure and Reflector Node Thickness¶
Two radial nodes are used in the reflectors and in the structure. The only restrictions on node thicknesses are that the total reflector thickness and the total structure thickness must be reasonable; 0.003 m or more, to prevent numerical instabilities in the temperature calculations in the boiling module. Usually, the node in contact with the coolant, the inner structure node or the outer reflector node, represents approximately \(10\%\) of the total thickness; and the other node represents the rest. Then the small node in contact the coolant will react rapidly to rapid changes in the coolant temperatures, whereas the larger node will dominate the longer-term response to the slow changes.
3.15.1.5. Coolant Re-entry Temperature¶
If PRIMAR-1 is being used, then the re-entry temperature calculation described in Section 3.3.6 uses the input variable TUPL for the bulk temperature of the coolant in the outlet plenum. If PRIMAR-4 is being used, then the outlet plenum temperature is computed by PRIMAR-4; and TUPL is not used.
3.15.2. Output Description¶
Figure 3.14.1 shows a typical thermal hydraulic output for one step of the transient. The output is largely self-explanatory. Note that on the first page of this output the axial location, coolant temperature, saturation temperature, and pressure are the values at node boundaries; whereas the cladding, structure, plenum, and reflector temperatures are the values at node mid-points. Also, on the second page the radial fuel temperatures are the values at node mid-points except for the inner and outer fuel temperature, as indicated in Figure 3.2.4; whereas the radii are the values of radial node boundaries.
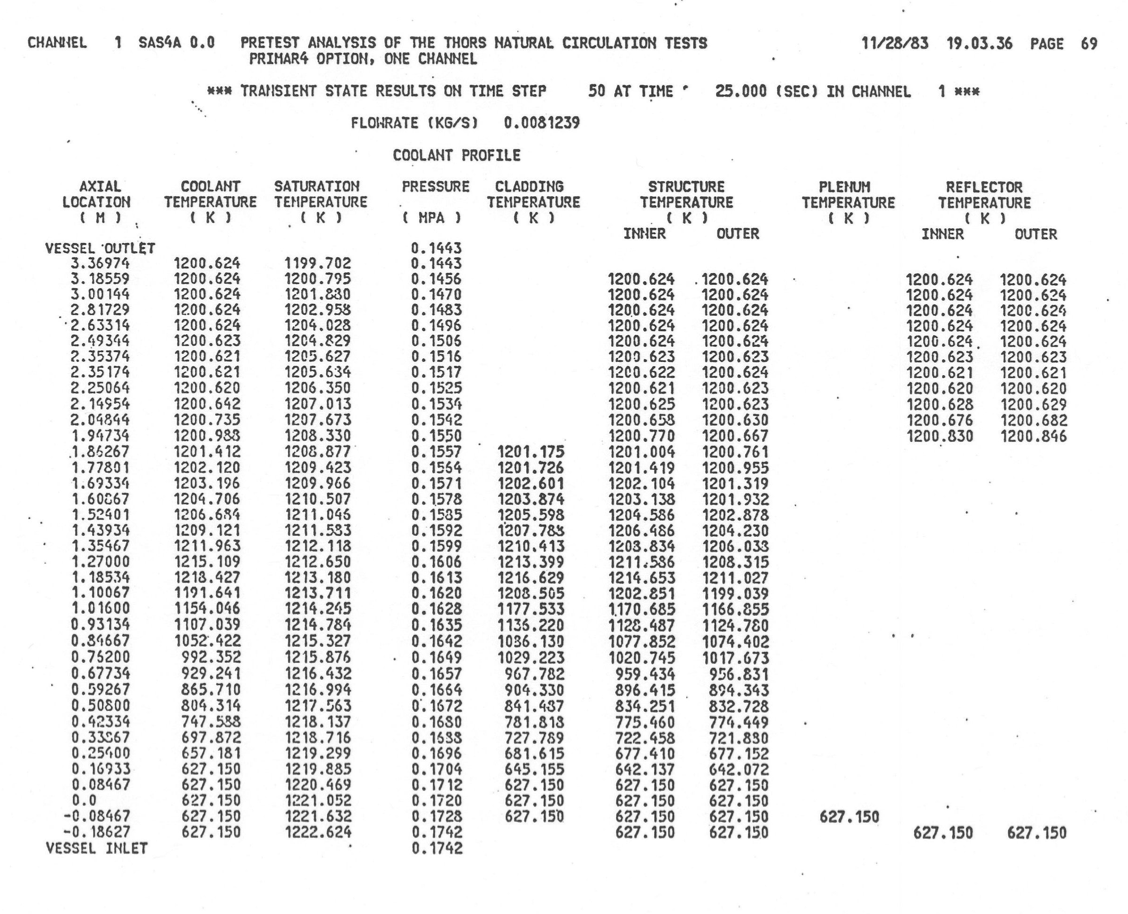
Figure 3.15.1 Sample Subassembly Thermal Hydraulics Output¶
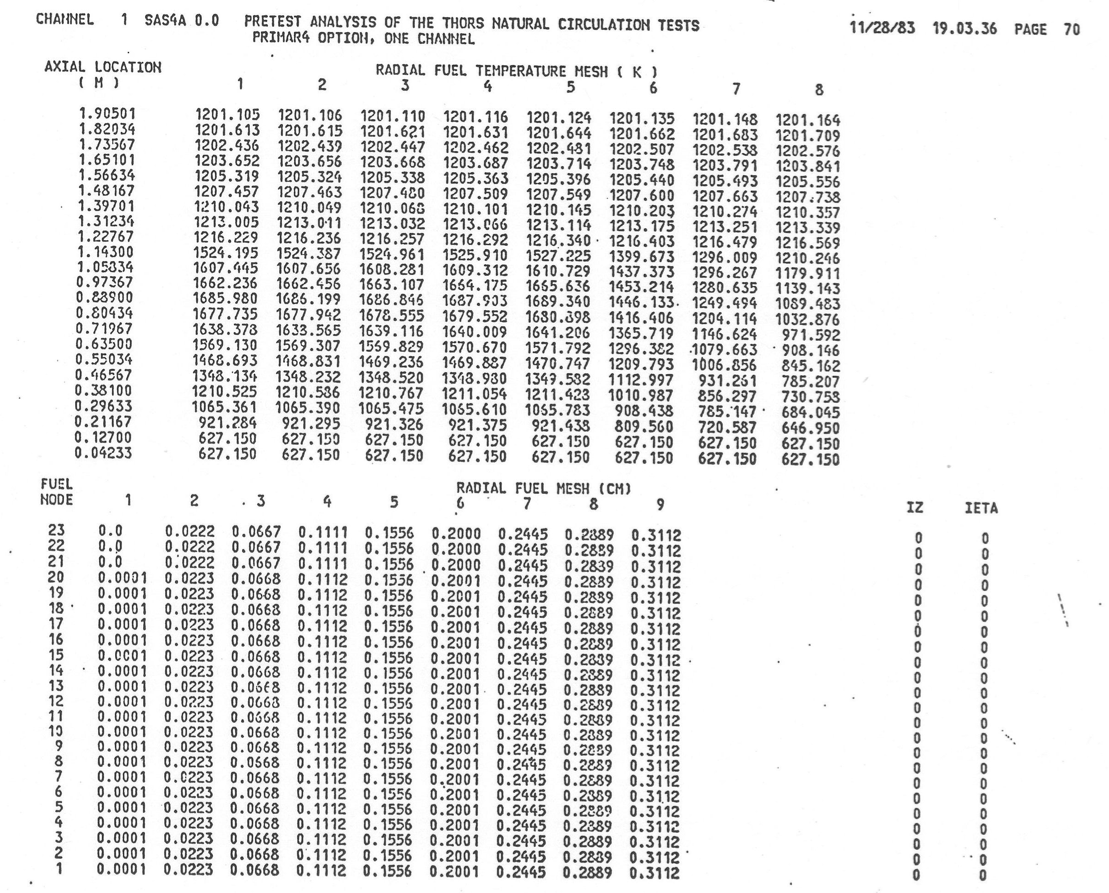
Figure 3.15.2 Sample Subassembly Thermal Hydraulics Output (Cont’d.)¶
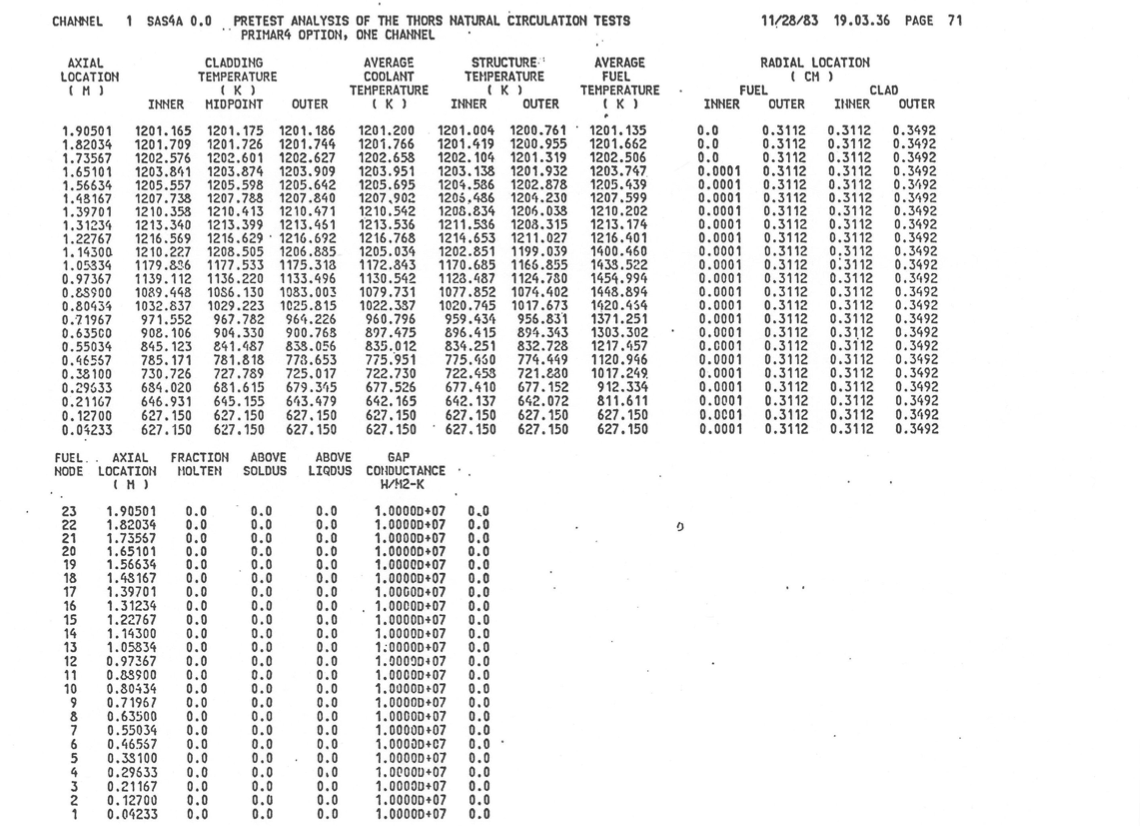
Figure 3.15.3 Sample Subassembly Thermal Hydraulics Output (Cont’d.)¶
3.15.3. Subchannel Information¶
This section provides additional information that is necessary to implement the subchannel model described in Section 3.14. This includes a brief user guide, followed by a sample problem, then a detailed overview of the required input. More information about the SAS4A/SASSYS‑1 preprocessor, which is available to expedite the input creation process for the subchannel model, can be found in Section 3.19.2.
3.15.3.1. User Guide¶
This user guide provides a quick summary of the grouping of channels and subassemblies and how to properly prepare the required input. Information about standard output and a binary plotting option is also given.
3.15.3.1.1. Channels, Subassemblies, and Groups¶
A basic feature of the core treatment is the concept of a channel. In simple terms a channel consists of a fuel pin and its associated coolant and structure. As used in the SAS4A/SASSYS‑1 code, a channel is a bit more involved. Figure 3.15.4 shows some details of a SAS4A/SASSYS‑1 channel if the three dimensional thermal hydraulics model is not being used. In the axial direction the whole length of the subassembly is modeled. A channel includes the whole fuel pin, including the fuel region, axial reflectors in the fuel pin, a gas plenum region at the top or bottom of the fuel pin. Also, a channel includes axial reflector zones above and below the fuel pins.
When the three dimensional thermal hydraulics model is used, the concept of a channel is even more involved. The three-dimensional treatment is used only in the pin section. Multiple channels are used in the pin section of a subassembly, but in the axial reflector zones a single channel treatment is used, as shown in Figure 3.15.5. The first channel used to represent a subassembly includes the pin section and the axial reflectors. All other channels used to represent the subassembly only include the pin section, as seen in Figure 3.15.6.
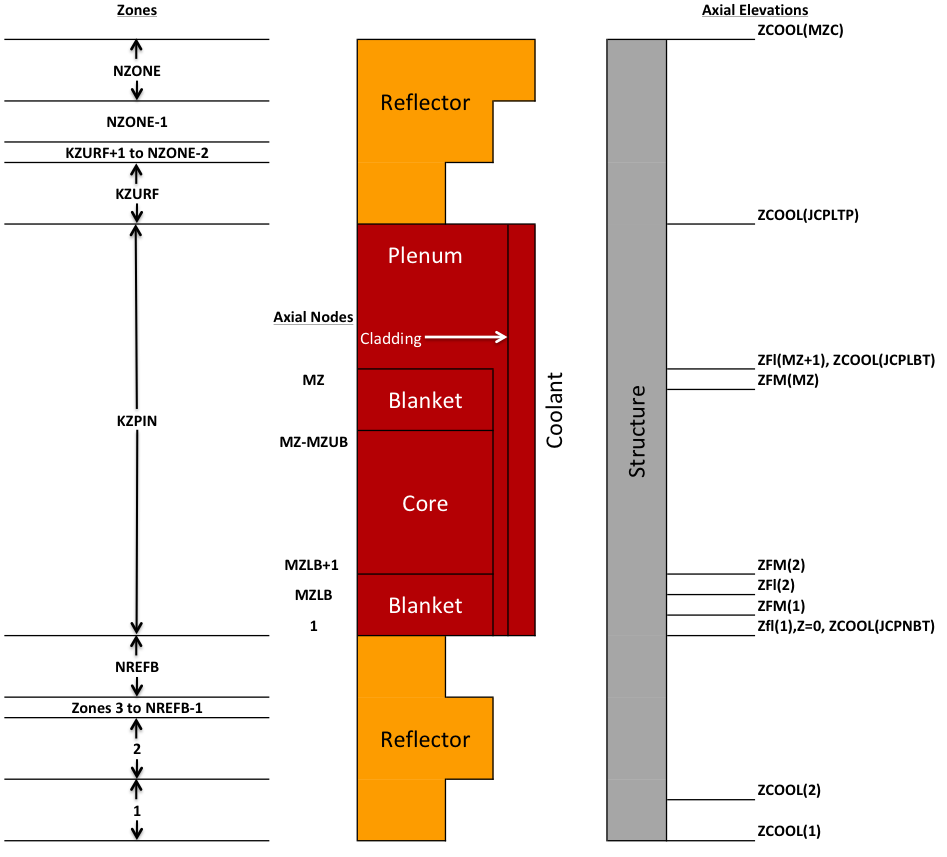
Figure 3.15.4 Details of SAS4A/SASSYS‑1 Axial and Radial Nodes (if 3-D Thermal Hydraulics Model is not Being Used)¶
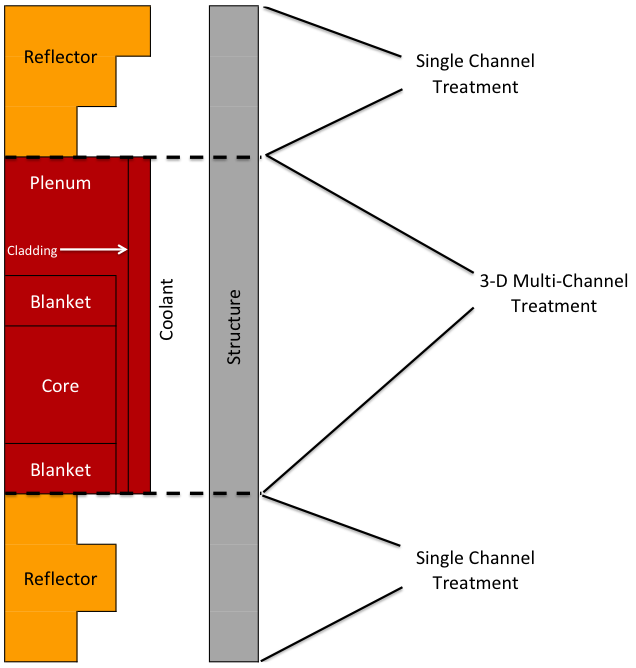
Figure 3.15.5 Breakdown of Axial Regions and Treatments¶
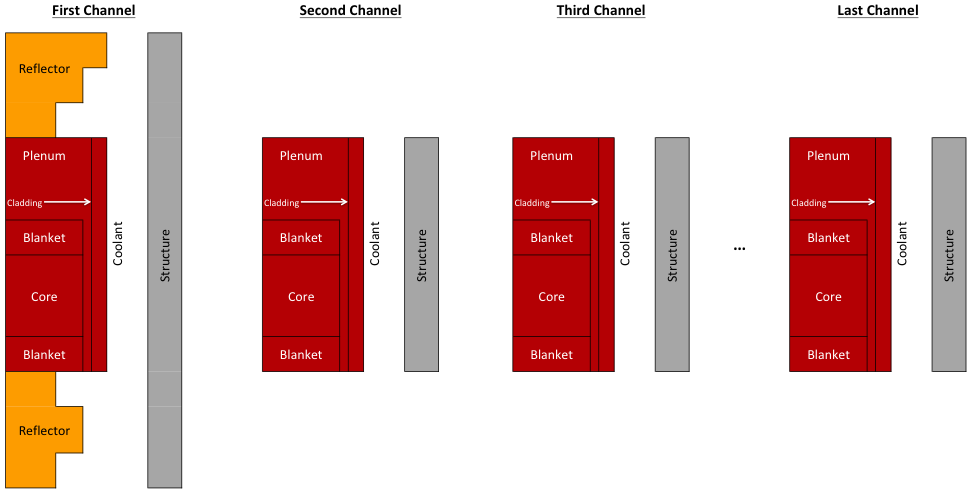
Figure 3.15.6 3-D Thermal Hydraulics Input Channel Structure¶
Coolant flow enters a single channel at the bottom of the subassembly, flows through a single channel in the lower reflectors, splits into multiple flow paths in the pin section, and re-combines into a single flow path for the upper reflectors, as shown in Figure 3.15.7. In the pin section, cross-flow between the channels representing a subassembly is accounted for.
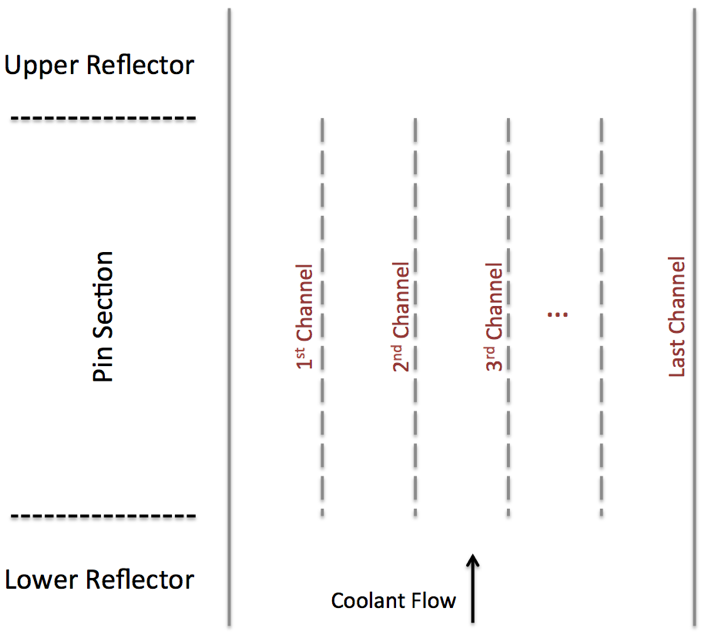
Figure 3.15.7 Subchannel Model Flow Diagram¶
If one is modeling a reactor without solid duct walls, then accounting for cross-flow between subassemblies is desirable. In order to handle this situation, the concept of a group of channels was incorporated in the model. If solid duct walls are used, then there will be a one-to-one correspondence between subassemblies and groups. If solid duct walls are not used then a group can include many subassemblies, maybe even the whole core. Cross flow between adjacent channels in the whole group is accounted for, but again cross flow is only accounted for in the pin section. The reflector zones are included only in the first channel in a group. Channels are still combined into subassemblies for some edits, even if multiple subassemblies are included in a group. The maximum number of channels that can be included in a group is limited only by the amount of computer memory available for temporary storage of coolant variables during the simultaneous solution of the coolant conditions in all channels in the group. This temporary storage memory is allocated dynamically at run time based on the maximum group size.
Subassembly numbers are assigned by the user by setting the input variable ISUBAS (location 89 of block 51). Group numbers are assigned by the code on the basis of input variable JJMLTP (location 214 of block 51). If JJMLTP for a channel is greater than or equal to zero, then a new group is started. If \(\text{JJMLTP} < 0\), then the channel is part of the current group.
3.15.3.1.2. Preparing Input for a Case¶
One issue to be addressed when preparing input for a case using the new three dimensional thermal hydraulics core model is the amount of detail to be used for various parts of the core. If enough computer memory and computer speed are available, then one could analyze every coolant subchannel and every fuel pin in the core. It is also possible to analyze some subassemblies with the detailed subchannel treatment shown in Figure 3.14.1, to analyze other subassemblies with a somewhat less detailed treatment such as that shown in Figure 3.15.8, and to analyze the rest of the core using one channel to represent a subassembly or a group of similar subassemblies.
The amount of input required for even a moderately sized case can be considerable. Some input is required for each channel, and the number of channels can easily be very large. Fortunately, most of the input for the new model is fairly repetitive, and much of it can be automated by a preprocessor. Section 3.19.2.3 describes a preprocessor that has been written for the SAS4A/SASSYS‑1 code with the new model.
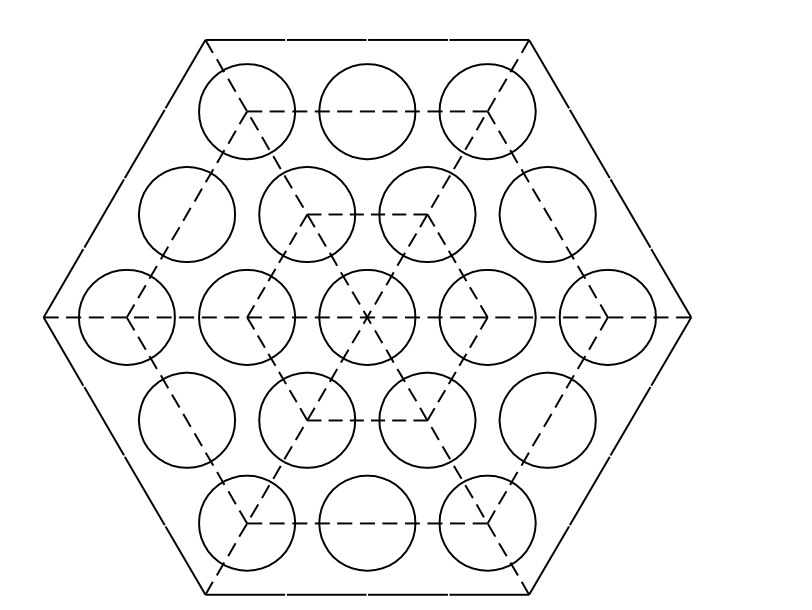
Figure 3.15.8 Subchannels Grouped in Rings¶
3.15.3.1.3. Controlling the Amount of Standard Output¶
The standard output from SAS4A/SASSYS‑1 includes tables of temperatures, pressures and coolant flow rates for each axial node and each radial node in each channel. These tables are printed out for the steady-state results and for every IPO (location 12, input block 1) time steps during the transient. Even before the new three-dimensional thermal hydraulic model was added to the code, the problem of excessive amounts of output from the code was recognized. An input variable, IPRSKP (location 274, block 51) can be used to skip output from specified channels. Also, before the new model was added to the code, reactivity feedback components for each channel were printed out for each step of the transient. Now the reactivity feedback components are printed out for each subassembly rather than for each channel.
3.15.3.1.4. Binary Output for Plotting¶
The new model includes a provision for writing a binary output file on unit 24. This output file can contain user specified values calculated by the new model. It is anticipated that plotting programs will use this file to plot results from the new model. The user can specify which data is included on unit 24, how often that data is written, and for which channels.
The SAS4A/SASSYS‑1 code writes a number of binary output files other than the unit 24 file mentioned above. The CHANNEL.dat binary file reports reactor power and reactivity feedback in addition to temperatures of fuel, clad, and structure, and coolant flow rates for all channels. The CHANNEL.dat file can be extremely large if using the subchannel model, as a full thermal hydraulic dataset is provided for each subchannel in the binary output. While the user cannot control what channels are included in CHANNEL.dat, the user can control the frequency of output using the MSTPLA, MSTPLB, MSTPL1, MSTPL2, and MSTPL3 (INPCOM:107-111) input fields.
3.15.3.2. Sample Problem¶
Figure 3.15.9 shows output from a sample problem run with the new model. This test case uses two 19 pin subassemblies with subassembly-to-subassembly heat transfer. Selected coolant temperatures from one of the subassemblies are shown in Figure 3.15.9. The transient was a simulated scram with a delayed pump trip and little natural circulation head in the primary loop. Temperatures drop rapidly due to the scram and then rise after the pump trip until enough buoyancy is established in the subassemblies to increase the flow rate and stop the temperature rise. Flow reversal occurred in the center subchannels from 22.5 seconds to 83.5 seconds in the transient. Flow reversal occurred in the edge subchannels from 22.0 seconds to 111.25 seconds.
The case described above used two subassemblies, each containing 19 pins and 42 coolant subchannels in the pin section. Four axial nodes were used in a lower reflector below the pin section, 24 axial nodes were used in the core, 6 axial nodes were used in the gas plenum region above the core, and 5 axial nodes were used in a reflector above the pins. A null transient of 50 steps with a time step of 1.0 second was used for each subassembly separately. Then a 50 step null transient using both subassemblies and subassembly-to-subassembly heat transfer was run with a time step of 0.5 seconds. Finally the regular transient was run for 1200 steps using a time step of 0.25 seconds. The null transients started with 35 iterations per step and got down to 2 iterations per step as they converged on a steady-state solution. The regular transient required between 12 and 21 iterations per step. The total running time was 867 seconds on a Sun Blade computer with a 500 MHz processor.

Figure 3.15.9 Results for a Scram with a Delayed Pump Trip¶
3.15.3.3. Input Description¶
Input for the SAS4A/SASSYS‑1 code is read into numbered locations in input blocks. Each input block has a name and a number. Below is a listing of the additional input variables that are used for the new three-dimensional thermal-hydraulic core model. A description of each input can be found in the User Guide in Chapter 2.
Variable |
Reference Eq. No. |
Input Variable |
Input Block |
Location Number |
Suggested Value |
External Reference |
---|---|---|---|---|---|---|
ISSNUL |
1 |
87 |
||||
ISCH |
1 |
115 |
||||
ISUBAS |
51 |
89 |
||||
JJMLTP |
51 |
214 |
||||
JCHMPN(K) |
51 |
215-218 |
||||
NUMKLT |
51 |
219 |
||||
KSWIRL |
51 |
220 |
||||
NULSTI |
51 |
221 |
||||
IFT24 |
51 |
495 |
||||
ILATF |
51 |
496 |
||||
NFT24 |
51 |
501 |
||||
JCFT24(K) |
51 |
502-521 |
||||
ITYPE24(K) |
51 |
522-541 |
||||
NULPT1 |
51 |
542 |
||||
3.14-7 |
UACHM1(K) |
64 |
197-200 |
|||
3.14-8 |
UACHM2(K) |
64 |
201-204 |
|||
ALATRL(K) |
64 |
205-208 |
||||
XKLAT(K) |
64 |
209-212 |
||||
DPLTLM |
64 |
213 |
||||
XKSWRL |
64 |
214 |
||||
DTNUL1 |
64 |
215 |
||||
EPSFLW |
64 |
216 |
||||
EPSTMP |
64 |
217 |
||||
EPSPRS |
64 |
218 |
1.0 |
|||
XCMPRS |
64 |
219 |
||||
XLINRT |
64 |
220 |