15.3. Computer Implementation¶
15.3.1. Detailed Logic Flow Description¶
This section describes in detail the logical sequence of the solution method used in PINACLE. The structure of the PINACLE driver as well as initiation and interfacing considerations have been presented in Section 15.1.2. Some information about the interaction between LEVITATE models was presented in Section 15.1.2.1 and the method of solution for the molten cavity model was described in Section 15.2.1. This section will use, and occasionally repeat some of this information in order to present a comprehensive picture of the general solution method. Some considerations about data management and time-step selection are also presented.
15.3.1.1. Data Management Considerations¶
Every time PINACLE begins calculations in a channel, the permanently stored information is retrieved from the data container and loaded in the common blocks. This operation is performed in the TSTHRM module. A number of arrays and other data, however, which can be calculated from the permanently stored variables, are not retained in the permanent storage. These data are recalculated in the routine PNSET2 every time PINACLE receives control in a certain channel, i.e., at the beginning of a heat transfer time step. These variables are stored in temporary common blocks, and kept only as long as PINACLE retains control in the channel. At the end of the heat transfer time step, when PINACLE returns control to TSTHRM, these variables are lost. Only the permanent common blocks are saved in the data container. This procedure is used in order to reduce the amount of storage required for SAS4A. The permanent PINACLE variables are stored in the block PLUC, which is also used by PLUTO2 and LEVITATE. Thus, when PLUTO2/LEVITATE are initiated, the cavity data calculated by PINACLE are automatically available for these models.
15.3.1.2. Logic Flow for Solution Advancement¶
As explained in Section 15.1.2.1 the PINACLE model describes the thermal-hydraulic events that occur inside the fuel pin cavity. During each time step PINACLE advances the solution by calculating the value of all variables at the end of the time step. The time-step selection is described in Section 15.2.6. The PINACLE calculation begins by advancing the solution for the radial cavity extension in each axial cell. This calculation is performed in the PN1PIN routine. This routine calculates the new fuel and fission gas masses in each axial cell and solves the mass conservation equations. Then the energy conservation equation is solved in each axial cell, providing the new fuel and fission gas temperature. Using the updated masses, temperatures and volumes, the PN1PIN subroutine calculates the new local pressures. The velocities are then calculated in the PN2PIN routine, which solves the momentum conservation equations for each staggered momentum cell. A separate momentum equation is used to describe the ejection of molten fuel into the upper plenum if this ejection has been initiated. PN2PIN also prints the regular PINACLE output if necessary.
Using the fuel distribution at the end of each time step PINACLE then calculates the new channel fuel reactivity. At the end of each primary step the axial fuel mass distribution is returned to the FEEDBK routine, as explained in Section 15.1.3.3.3. Finally, when the end of the heat-transfer time step is reached, PINACLE calls the routine HTRVPN, which calculates the new temperatures in the solid fuel pin at all axial locations. These temperatures will be used in the next time step in the PN1PIN routine to calculate the new cavity diameter and the heat flux between the molten fuel and the cavity wall.
15.3.1.3. Time-step Considerations¶
The PINACLE driver routine, PINACL is called by the SAS4A transient driver TSTHRM at the beginning of each heat-transfer time step during a primary loop time step. The primary time step is common for all SAS4A calculation channels and is always smaller than or equal to the main time step used in the point kinetics calculation.
When in-pin fuel motion is detected in a given channel, the PINACLE time, TIMEPN, is set to zero in the CAVMOT routine. TIMEPN is initially advanced by adding the PINACLE minimum time step DTPNIN to the time TIMEPN. Subsequently, the time TIMEPN will be advanced by the time step calculated by PINACLE, as described below.
A hydrodynamic time step DTPI, is calculated first for the in-pin hydrodynamic model, as outlined in Section 15.2.6. This time step is then compared with the present maximum value \(1.10^{-3}\) s which is used to avoid numerical heat transfer instabilities. The smallest value is retained as the PINACLE time step. This value is further compared with the input minimum time step, DTPNIN and the larger value is retained. Finally, the PINACLE time step can be cut back if the newly determined time:
exceeds the end of the heat-transfer time step. In this case, the new PINACLE time step will be reduced so that the new PINACLE time \(t_{\text{PN}}^{n + 1}\) will coincide with the end of the heat-transfer time step.
As shown in the flow diagram 15.1-5, PINACLE retains control and advances the solution in a given channel until the end of a heat transfer time step is reached.
15.3.1.4. List of PINACLE Routines¶
This section contains a list of all the subroutines that are part of the PINACLE model:
Name |
Description |
---|---|
CAVMOT |
Decides when to initiate PINACLE calculations. This routine is called at the end of each heat transfer time step from DFORM3. |
PNINIT |
Sets several important PINACLE variables and calls the initialization routines PNIPT and PNSET. This routine is called from CAVMOT. |
PNINPT |
This routine is used together with PNSET to initialize the PINACLE variables. It is called from PNINIT. |
PNSET |
This routine is used, together with PNINPT, to initialize the PINACLE variables. It is called from PNINIT. |
PINACL |
PINACLE driver routine. It is called at the end of each heat transfer time step from TSTHRM. |
PN1PIN |
Solves the mass and energy conservation equations in the pin cavity. Also calculates the radial cavity expansion. It is called each PINACLE time step from PINACL. |
PN2PIN |
Solves the momentum conservation equations in the pin cavity. Also determines the next PINACLE hydrodynamic time-step and prints the regular PINACLE output. It is called every PINACLE time step from PINACL. |
HTRVPN |
Heat transfer routine active after PINACLE initiation. Calculates the transient temperatures in the solid fuel pin and cladding. It is called from PINACL at the end of each heat transfer time step. |
15.3.2. Input Parameters Relevant to PINACLE¶
The input parameters relevant to PINACLE are summarized in Table 15.3.1. The description of these parameters has also been included in the SAS4A input listing. Table 15.3.1 lists the recommended values for these parameters and the sections and equations where those parameters are mentioned in the text. The list of equations is not necessarily exhaustive, and some input parameters might appear in other equations, in addition to those listed in the table (e.g., AXMX appears in many places and it was not possible to list all occurrences).
Input Loc. |
Var. |
Sect. |
Eq. |
Sug. Value (MKS) |
Comments |
---|---|---|---|---|---|
Block 1, INPCOM |
|||||
49 |
INAPN |
0 |
If INAPN = 1 then PINACL will assume that small amounts of liquid sodium are present to each axial cell in the cavity. The sodium vapor pressure will be added to the local pressure, depending on the value of CINAPN (13/1286). This input is now provided for parametric studies. The modeling of the sodium field in the cavity will be added to PINACLE at a later time. If INAPN = 0 no sodium pressure is added to the cavity pressure. |
||
Block 13, PMATCM |
|||||
1277 |
DTPNIN |
\(2 \times 10^{-5}\) |
Minimum time step. |
||
1279 |
DTPNP |
0.05 |
Determines the time interval between PINACLE printouts. |
||
1286 |
CINAPN |
1 |
Determines the fraction of the sodium vapor pressure to be added to the local pressure. Can have values between 0 and 1. If CINAPN = 0 all the local sodium vapor pressure is added to the local pressure. If CINAPN = 1 then only the excess Pna (T:sub:na) - Plocal is added to the local pressure. |
||
1295 |
CIPNTP |
0.5 |
This variable controls the calculation of the fuel pin top boundary temperature, which is important in triggering the axial in-pin fuel relocation. Can vary between 0 and 1. If 1, the boundary temperature is the same as the temperature of the central top fuel mode. If 0, the boundary temperature is equal to the temperature of the material in the mode above the active fuel, i.e. sodium or blanket fuel central mode. |
||
1296 |
ROGSPI |
17.74 for U‑Fissium |
Mass of fission gas generated in the fuel pin per unit volume of the original pin and percent burnup. Kg/m3 fuel/% B.U. |
||
Block 51, INPCHN |
|||||
190 |
IPNPLT |
1 |
Controls the fuel distribution printer plot from PINACLE. Can be 0 or 1. If 1, the printer plot will be printed with each PINACLE printout. |
||
194 |
IPNGO |
The variables IPNGO, IPNSTP and IPNNEW can be used to obtain more frequent PINACLE output between the cycles IPNGO and IPNSTP. The PINACLE output will be printed every IPNNEW cycles. |
|||
195 |
IPNSTP |
||||
196 |
IPNNEW |
||||
Block 65, FUELIN |
|||||
22 |
FPINAC |
0.2 |
Controls the PINACLE initiation. The PINACLE calculations can only start in a channel where the maximum areal melt fraction (defined as FNMELT times the heat of fusion) is greater than FPINAC. See also CPINAC (65/23) and FNMELT (13/1169). |
||
23 |
CPINAC |
0.5 |
In addition to the FPINAC condition, PINACLE will start only if there are at least 3 adjacent cells with a melt fraction larger than CPINAC * FPINAC. |
||
52 |
FUSLDT |
Geometry dependent |
Specified the length of possible free motion for the blanket fuel stack and/a liquid sodium. If only liquid sodium is present it should be set equal to the plenum length. |
||
53 |
FUSLMA |
Specifies the mass of the blanket pellet stack and/or sodium which will have to be displaced when the axial fuel relocation begins. This mass refers to one pin only. |
|||
54 |
BURNFU |
Specifies the atom percent burnup for the fuel pins in the channel. It is used in the fission gas calculations when DEFORM-4 is not active. |
15.3.3. Output Description¶
15.3.3.1. Regular Output¶
The PINACLE output has been designed to provide the essential information about the fuel pins in the channel at a given point in time. The output is printed from PINACL and can be obtained at equal time intervals, by specifying the input integers IPNGO, IPNSTP and IPNNEW. The PINACLE output will then be printed between cycles IPNGO and IPNSTP every IPNNEW cycles.
The regular PINACLE output is illustrated in Figure 15.3.1. The first line in the pin-related output contains the computational cycle number ICYCLE, the SAS4A channel number ICH and the current time, TIMEPN. This time is measured from the initiation of the in-pin fuel motion calculations in the given channel.
The second line contains some summary information about the fuel pin cavity and the status of the axial fuel ejection above the active fuel column. All the masses in this line refer to the whole subassembly:
Variable |
Description |
---|---|
FUSLDB |
Length of molten fuel column ejected above the active fuel pin, m. |
SMFUCA |
Total mass of molten fuel in the pin cavity, kg. |
SMFICA |
Total mass of free fission gas in the pin cavity, kg. |
SMFSCA |
Total mass of dissolved fission gas in the pin cavity, kg. |
SMFUME |
Total mass of pin fuel that has molten since PINACLE initiation, kg. |
SMFIME |
Total mass of free fission gas released to the cavity due to fuel melting, kg. |
SMFSRT |
Total mass of fission gas that was originally dissolved in the molten fuel but was released in the meantime, kg. |
TEPNTP |
Temperature of the active fuel column top interface. The axial fuel ejection of the fuel from the cavity into the plenum is initiated only after this temperature reaches the fuel solidus temperature, K. |
PRPLNM |
Current pressure in the pin plenum (Pa). If the blanket stack did not reach a rigid obstacle, i.e. FUSLDB < FUSLDT, the difference between this pressure and the pressure in the top cavity cell controls the axial fuel ejection. |
Two groups of columns follow, providing more detailed information for all axial cells in the cavity. These columns are described below. Whenever masses are involved they refer to a single pin, rather than to a whole subassembly.
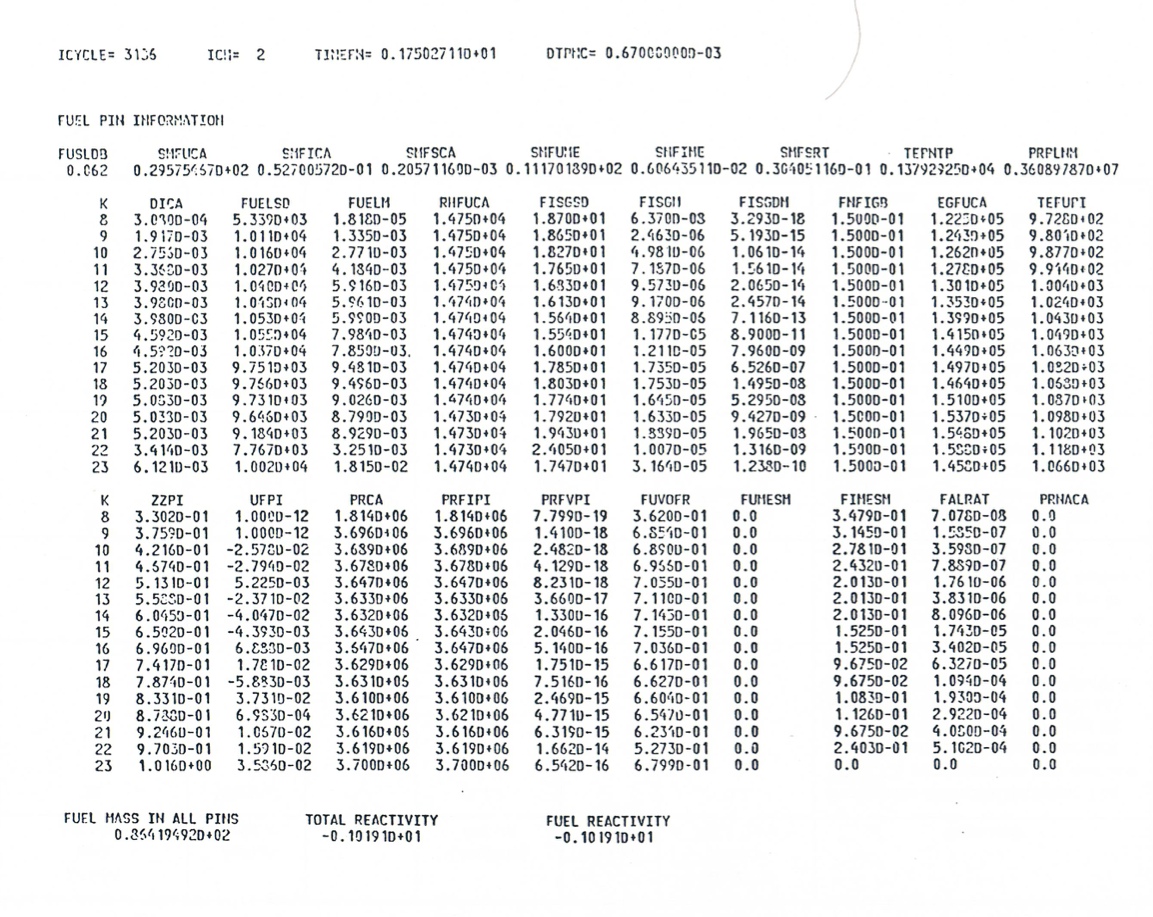
Figure 15.3.1 Regular PINACLE Output¶
First group of columns:
Variable |
Description |
---|---|
K |
The number of the axial cell in the cavity. This number refers to the cavity grid, which differs from the channel grid by the integer IDIFF, i.e., K=I - IDIFF. |
DICA |
Diameter of the cavity, m. |
FUELSD |
Molten fuel density smeared over the cavity area, kg/m3. |
FUELM |
Molten fuel mass, kg. |
RHFUCA |
Physical density of the molten fuel, kg/m3. |
FISGSD |
Free fission-gas density, smeared over the cavity area, kg/m3. |
FISGM |
Free fission-gas mass, kg. |
FISGDM |
Dissolved fission-gas mass, kg. |
FNFIGB |
Fraction of the fission gas which is released instantaneously upon fuel melting. This fraction is currently an input constant, independent of the axial location. |
EGFUCA |
Enthalpy of the molten fuel in the cavity, J/kg. |
TEFUPI |
Temperature of the molten fuel, K. |
The second group of columns:
Variable |
Description |
---|---|
K |
The number of the axial cell in the cavity. |
ZZPI |
Axial location of the lower boundary of cell k, measured from the bottom of the pin, m. |
UFPI |
Velocity of the molten fuel/fission gas-mixture in the cavity, at the axial location ZZPI, m/s. |
PRCA |
Total pressure in the cavity, Pa. |
PRFIPI |
Partial pressure of fission gas in the cavity, Pa. |
PRFVPI |
Partial fuel vapor pressure in the cavity, Pa. |
FUVOFR |
Molten fuel volume fraction in the cavity. |
FUMESM |
Mass of fuel molten during the current time step, kg. |
FIMESM |
Mass of free fission gas added to cell K of cavity during the current time step, kg. |
FALRAT |
Failure ratio used to determine the initiation of cladding failure and switching to PLUTO2 or LEVITATE models. Cladding failure occurs when FALRAT ≥ 1 in any axial node. |
PRNACA |
Partial pressure of sodium vapor in the cavity, Pa. |
Finally, a last summary line prints the fuel mass in all the pins in a subassembly and the total reactivity introduced by the molten fuel relocation calculated by PINACLE. The reactivity effect refers to the whole SAS4A channel, i.e., accounts for the number of assemblies grouped together in a SAS4A channel.
15.3.3.2. Optional Output¶
An optional printer plot of the axial fuel distribution in a channel can
be obtained by setting the input IPNPLT
= 1. This optional
output is illustrated in Figure 15.4.1.
This plot prints the linear fuel density in g/cm for each axial cell. Note that the cell numbers that appear on the left refer to the coolant channel mesh, not to the fuel pin mesh. The ordinate indicates the linear density at each axial location in g/cm/pin. It is generally labeled in increments of 0.5 g/cm. The symbol “T” indicates the total amount of fuel at each location, while the “P” indicates the amount of solid fuel at the same location. The difference between the “T” and “P” values is thus a measure of the amount of molten fuel present at the location. Finally, the original amount of fuel at each location is marked by a “0”. At locations where the total amount of fuel present “T” is the same as the original amount of fuel “0”, only the “T” appears.