15.4. Future Directions for Modeling Efforts.¶
15.4.1. Annular Molten Region¶
The current version of PINACLE models the formation of circular central cavity within the fuel pin and the subsequent fuel relocation inside this central cavity. Although the formation of such a central cavity is likely in U-F metal pins and oxide fuel pins, the situation is different for the U-Pu-Zr pins currently considered for the metal fuel core. In the U-Pu-Zr pins the material redistribution, particularly the Zr migration, leads to the formation of an annular Zr-depleted region, with a melting point significantly lower than the central and outer fuel regions. As the fuel pin temperature increases, the SAS4A calculations for U-Pu-Zr pins may indicate the formation of an annular molten cavity, due to the presence of this annular region with a low melting temperature.
It is thus necessary to develop a PINACLE capability to treat the formation of an annular cavity and to model the hydrodynamic fuel relocation in an annular geometry. Furthermore, the heat transfer model HTRVPN will have to be changed to accommodate the heat transfer calculations in the central solid region and annular molten cavity. Once this capability is developed it will be possible to use the results calculated by the fuel redistribution modules, to obtain a more complete picture of the U-Pu-Zr fuel pin behavior during the accident.
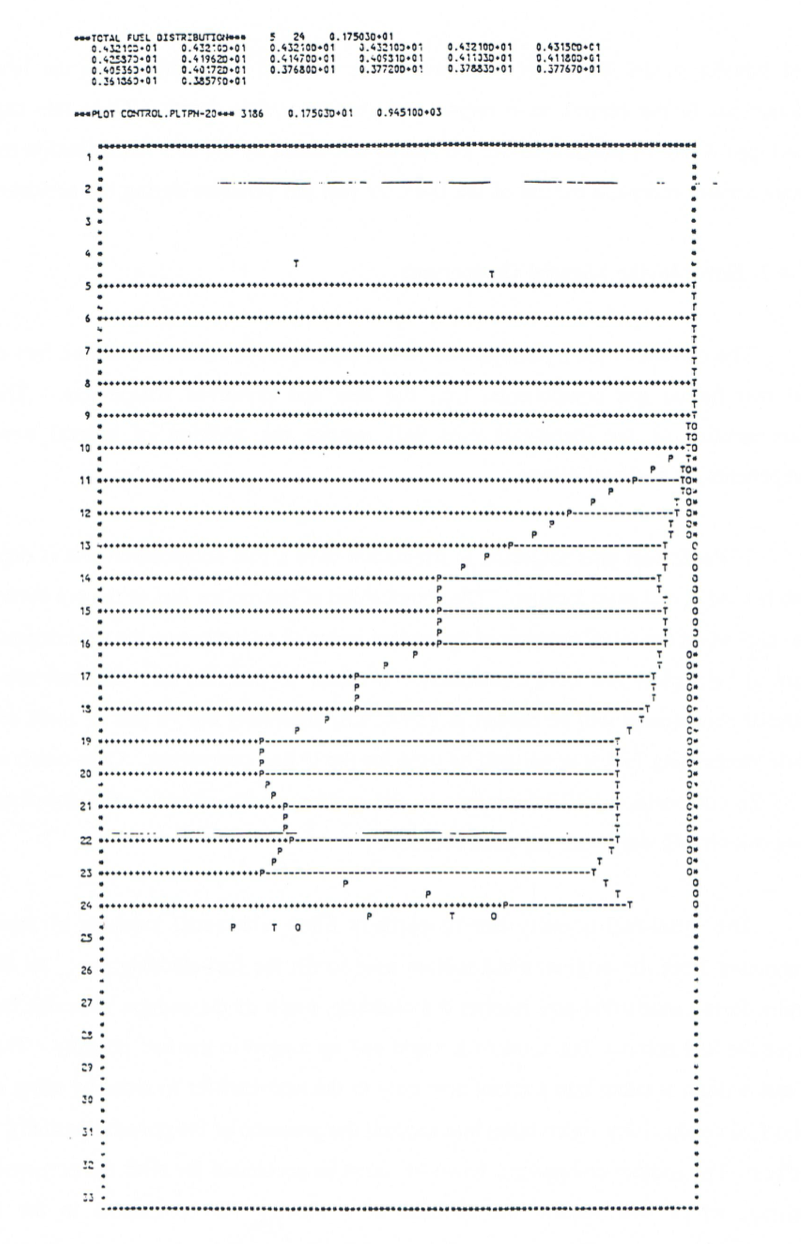
Figure 15.4.1 Optional PINACLE Output¶
15.4.2. New Moving Material Components¶
The current in-pin hydrodynamic model describes the relocation of one fuel component and two fission gas components, i.e., the free and dissolved fission gas. The specific characteristics of the metal-fuel pins will require the addition of several new material components, as outlined below.
U-Pu-Zr fuel pins subjected to irradiation have a fuel composition that is dependent on both the radial and axial location. The composition of the molten fuel in the pin cavity will thus also depend on the initial location of the molten material, as well as on the time dependent in-pin material relocation and cavity extension. In order to describe this situation two new fuel material components will be needed in PINACLE, describing the Pu and Zr mass distribution, while the existing fuel material will be used for the U fuel component. Only one homogenized U-Pu-Zr composition will be present in the molten cavity at each axial location, but this composition will vary with the axial location.
The metal-fuel porosity can be partially filled with small amounts of liquid sodium originating from the original bond sodium used to fill the fuel-cladding gap. As the fuel pin swells during irradiation and reaches the cladding, much of the sodium relocates in the space above the fuel column, but some of it might end up logged in the fuel porosity. The presence of this sodium is taken into account now only in the heat-transfer models, by using a modified solid fuel conductivity which takes into account the presence of the porosity partially filled with sodium. The sodium component, however, must be accounted for after the occurrence of fuel melting, which will require the addition of a moving Na component to the PINACLE hydrodynamic model. The presence of the liquid sodium in the molten cavity will directly affect the physical properties of the moving mixture. Although at the pressure levels prevailing in the bottled cavity the liquid sodium is not expected to have a major effect on the pressure, this situation can change after the pin failure when the cavity pressure drops rapidly and the sodium vapor pressure might play a significant role. Adding the liquid Na component to the PINACLE hydrodynamic model will allow the modeling of the prefailure in-pin axial sodium relocation and will provide the correct initial conditions for the postfailure LEVITATE calculations.
A characteristic phenomenon in metal-fuel pins is the formation of a molten eutectic layer at the fuel cladding interface. Iron diffuses inwards into the fuel, leading to the formation of an alloy with a lower solidus temperature than the original fuel and thus to fuel liquefaction. This molten eutectic region progresses radially at the same time as the central molten fuel cavity. When the molten fuel region reaches the molten eutectic region the two molten components can mix and axial relocation of the molten eutectic is possible. This situation is not modeled currently. Although the formation of the cladding molten eutectic region is taken into account in the DEFORM-5 cladding failure calculations, the iron present in the molten fuel or cladding cannot relocate axially or mix with the molten fuel. A moving cladding material component will be needed in the PINACLE hydrodynamic model in order to model the molten fuel and cladding mixing and axial relocation. The fuel and cladding components interact chemically, resulting in a mixed molten alloy. The mixing and interaction of the fuel and cladding directly affects the physical properties of the molten moving mixture. The axial relocation of the molten cladding material itself is expected to have a small reactivity effect prior to cladding failure but, more importantly, it will provide the correct initial conditions for the postfailure fuel relocation, when rapid in-pin motion can lead to more significant reactivity effects due to in-pin cladding relocation.
15.4.3. Inner Cladding Ablation¶
In metal-fuel pins the molten material region can extend radially past the original inner cladding interface as the molten fuel region is connected to the molten eutectic region. At present, the molten cavity can extend only to the initial inner cladding interface and cladding ablation can occur only at the outer cladding interface, after the initiation of the postfailure fuel motion model LEVITATE. When the molten cladding moving component is implemented, a model describing the cladding ablation at the fuel-cladding interface will be necessary. This model will allow the radius to increase past the original inner cladding radius and will allow the mixing of the molten eutectic with the moving components in the pin cavity as needed.
15.4.4. Composition-Dependent Moving Mixture Properties¶
The physical properties of the molten mixture in the cavity are dependent on the material composition, i.e., the proportion of U, Pu, Zr and Fe in the mixture. The physical properties affected by the composition include the solidus and liquidus temperatures, the conductivity, specific heat and density. Composition dependent functions representing these physical properties will have to be implemented in the PINACLE routines.
15.4.5. Fuel Freezing in the Plenum¶
The present model describes the radial heat-transfer between the fuel ejected above the fuel-pin and the cladding. The heat-transfer model will be expanded to describe the axial heat transfer between the molten fuel and the liquid sodium slug. A fuel freezing model describing the formation of a fuel crust in the gas plenum is already available in PINACLE. However, the accuracy of this model is limited by the fact that only one axial fuel cell, of variable length, is allowed above the molten fuel-pin. This limitation was introduced mainly because of the limited number of axial locations (24) available in SAS4A for the fuel-pin arrays. In the future the models describing the molten, heat-transfer and freezing of the ejected fuel will be expanded by allowing the fuel region to cover multiple axial cells located above the original fuel pin. A precondition for this development is an increase in the size of the SAS4A fuel-pin arrays.
15.4.6. Initiation of Axial Motion¶
The results of the TREAT experiment analyses performed with PINACLE, such as TS-2, M2 and M3 series indicate that the temperature of the fuel pin top interface is an important element for the prediction of the time of onset of axial fuel ejection. However, it is likely that the pressure difference between the molten fuel cavity and the upper gas plenum also plays a role in the initiation of axial fuel ejection. The model describing the onset of fuel motion will be enhanced in the future to incorporate both the interface temperature and pressure difference effects.
The timing of the in-pin molten fuel relocation initiation plays an important role in determining the accident sequence. If the in-pin fuel motion is initiated prior to cladding failure, a significant amount of negative reactivity is added at a high rate, causing a rapid decrease in power and reactivity. Thus, if cladding failure occurs later, it is likely to occur at considerably lower power and reactivity levels. The timing of the rapid in-pin fuel relocation initiation is determined by the breach of the solid fuel at the top of the pin, which separates the molten pressurized cavity from the gas plenum, usually at a lower pressure. This event is influenced both the temperature distribution near the top of the fuel pin and by the pressure difference between the molten cavity and the gas plenum.
As present the fuel temperatures in the top axial fuel cell are used to determine the timing of the onset of rapid in-pin fuel relocation. Only a radial fuel distribution is calculated and any axial heat transfer is neglected. However more detailed two-dimensional calculations indicate that near the top of the fuel pin the axial heat transfer between the fuel and the molten sodium present above the fuel pin becomes an important element in determining the temperature distribution. Because the top of the solid fuel pin actually controls the onset of rapid in-pin molten fuel relocation, it is necessary to implement at two-dimensional temperature calculation in the top axial fuel cell.
It is likely that the pressure difference between the molten cavity and the upper gas plenum also plays a role in the initiation of the axial fuel upward ejection. The current models do not take into account this pressure difference in the initiation of in-pin rapid fuel relocation, although the pressure difference is considered in the hydrodynamic models and plays an important role in determining the rate of fuel ejection after the onset of in-pin fuel relocation. The model describing the onset of rapid molten fuel motion will be enhanced in the future to incorporate the pressure difference effects in addition to the fuel temperature distribution.
15.4.7. Fuel Blanket and Sodium Slug Motion¶
A separate momentum equation describing the motion of the fuel blanket stack and/or liquid sodium slug will be added. Currently, this stack is modeled as moving together with the molten fuel until it reaches a rigid obstacle. Afterwards, the stack is assumed immobile and the fuel ejection is governed by the pressure difference between the upper cavity cell and the cell above the fuel pin. Although the current treatment is physically justified and necessary, for numerical stability reasons, when the amount of molten fuel ejected is small, the addition of a separate momentum equation for the pellet stack and/or liquid sodium slug will significantly increase the flexibility of the model when calculating the ejection of larger amounts of molten fuel above the active fuel column.
At present, the calculations describing the transient temperatures of the liquid sodium slug and fission gas plenum continue after the initiation of the rapid in-pin fuel relocation, ignoring the boundary heat-transfer changes due to the sodium slug relocation.
In fact the sodium slug is moving upwards, and thus the surrounding cladding temperatures change, leading to different heat fluxes. In addition, the axial heat transfer occurring at the lower slug boundary between the liquid sodium and molten fuel is likely to be significant. In the case of the fission gas, the upward motion of the sodium slug causes a decrease of the fission gas volume and boundary area. While the volume decrease is now accounted for in the pressure calculations, the heat-transfer model must be modified to account for the changes in the cladding area in contact with the plenum gas.
15.4.8. PINACLE Termination Upon Fuel Freezing and Restart Upon Remelting¶
For the examination of transients with decreasing power levels after the initiation of PINACLE, the addition of the capability of modeling fuel freezing in the pin cavity will also be necessary. In order to allow the analysis of long transients even after PINACLE has been initiated, it is necessary to develop the capability of discontinuing the PINACLE calculations whenever the fuel in the pin cavity freezes again and restarting the PINACLE calculations at a later time if necessary. This will allow the SAS4A calculations to proceed with significantly larger time steps.