3.2. SAS4A/SASSYS‑1 Channel Approach¶
SAS4A/SASSYS‑1 is capable of using a multi-channel treatment. Each channel represents a fuel pin, its associated coolant, and a fraction of the subassembly duct wall, as indicated in Figure 3.2.1. Usually, a channel is used to represent an average pin in a fuel subassembly or a group of similar subassemblies. A channel can also be used to represent a blanket assembly or a control-rod channel, and the hottest pin in a subassembly can be represented instead of the average pin. Different channels can be used to account for radial and azimuthal power variations within the core, as well as variations in coolant flow orificing and fuel burn-up. In the multiple pin option, more than one channel can be used to represent a subassembly.
3.2.1. Axial Mesh Structure¶
A channel usually represents the whole length of the subassembly, from coolant inlet to coolant outlet. A number of axial zones are used, as indicated in Figure 3.2.2. One zone represents the fuel-pin section, including the core, axial blankets, and gas plenum. Other zones represent reflector regions above and below the pin section. A maximum of 7 zones can be used in a channel. In general, radial dimensions and thermal properties are constant with a reflector zone. The pin section zone is treated separately in considerably more detail than the reflector zones. The gas plenum can be either above or below the core.
Figure 3.2.3 shows the axial mesh structure used for a channel. The coolant and structure nodes run the whole length of the channel. The coolant nodes are staggered with respect to the fuel, cladding, reflector, and structure nodes. Using coolant temperatures defined at the axial boundaries between cladding and structure nodes makes it easier to calculate accurate coolant temperatures. If non-uniform axial mesh sizes are used, a simple finite differencing of the coolant temperature equation gives accurate coolant temperatures with a staggered mesh, whereas if the coolant nodes were at the middle of the cladding nodes, then obtaining accurate coolant temperatures would require extra terms in the finite differencing of the coolant temperature equation.
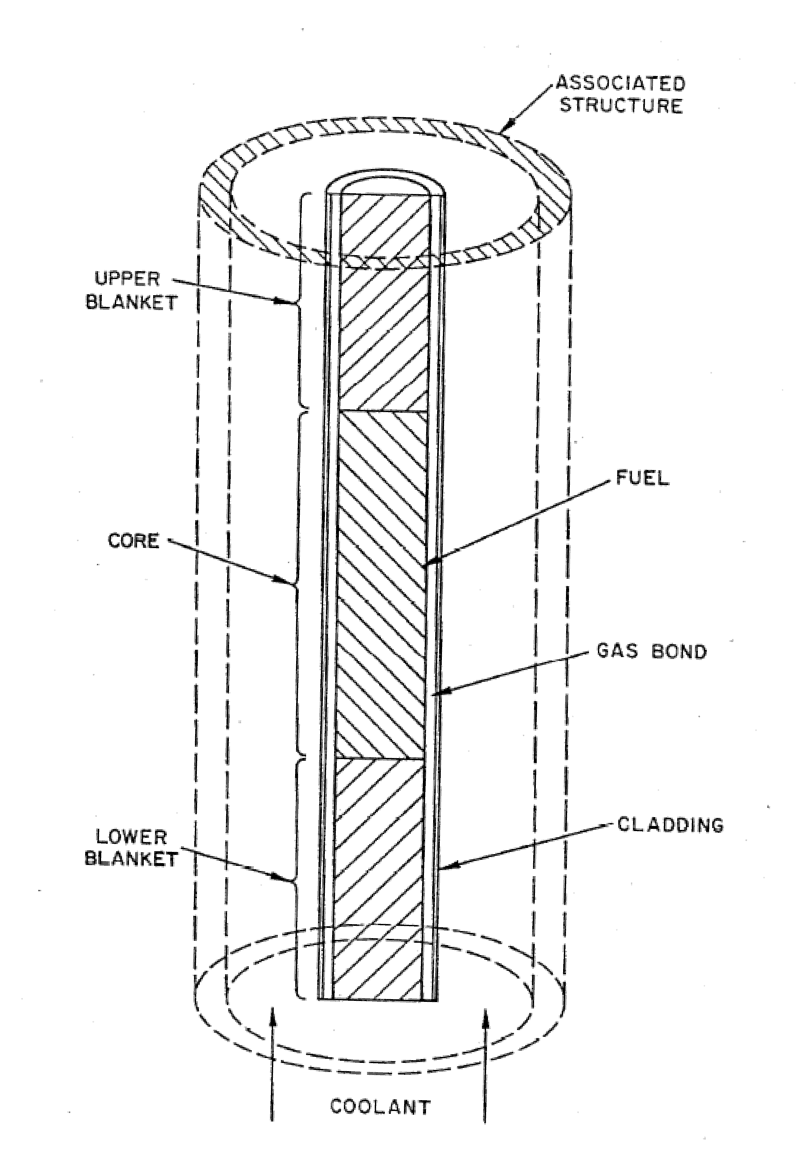
Figure 3.2.1 SAS4A/SASSYS‑1 Channel Treatment¶
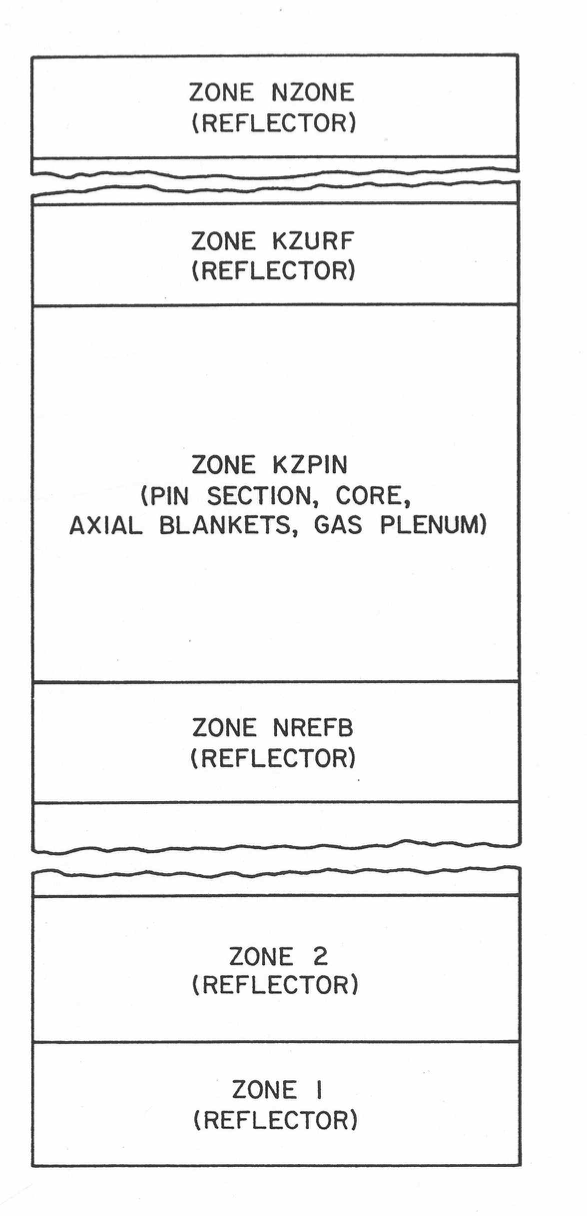
Figure 3.2.2 Axial Zones in a SAS4A/SASSYS‑1 Channel¶
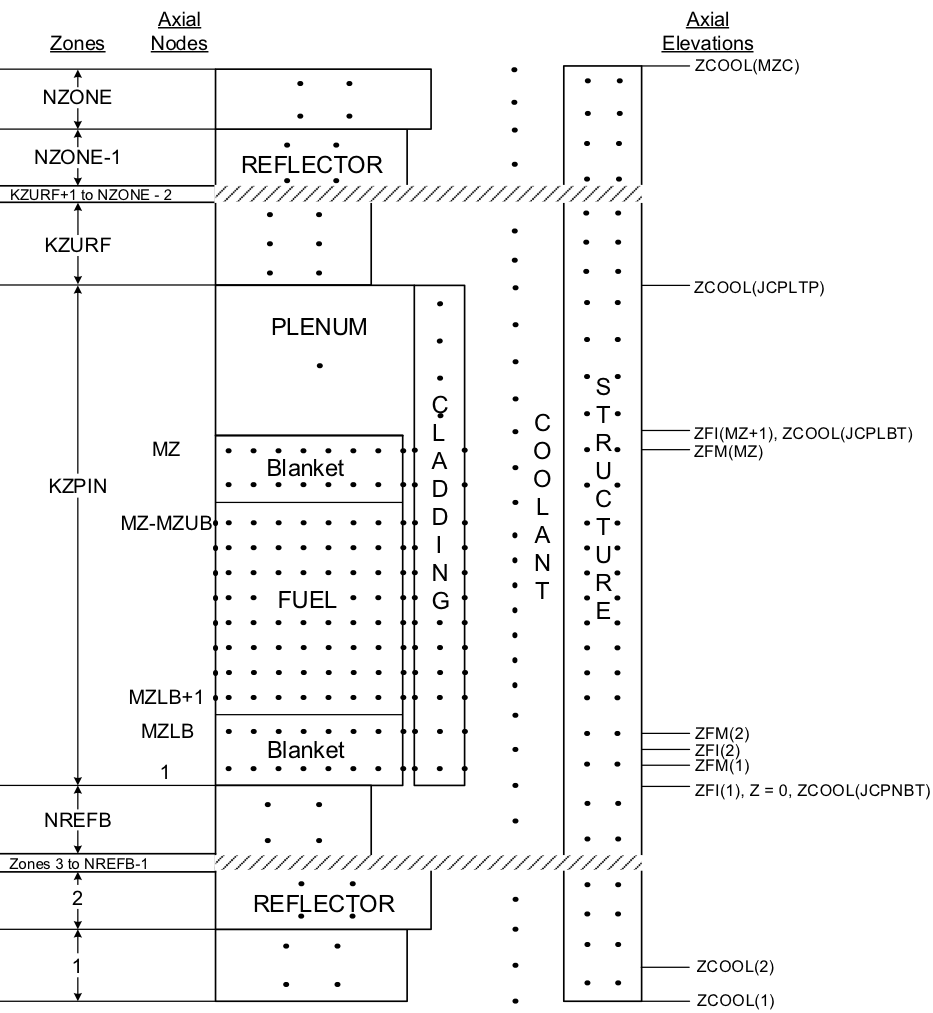
Figure 3.2.3 Schematic of SAS4A/SASSYS‑1 Channel Discretization¶
3.2.2. Radial Mesh Structure¶
3.2.2.1. Core and Blanket Region¶
Figure 3.2.4 shows the radial mesh structure used for temperature calculations in the core and blanket regions. This figure represents one axial node. Between four and eleven radial nodes are used in the fuel, three in the cladding, one in the coolant, and two in the structure. In the fuel, the nodes can be set up on either an equal radial difference basis or an equal mass basis. In either case, the first and last nodes are half-size. For a given number of nodes, an equal radial difference mesh will usually give more accurate center-line temperatures, but equal mass nodes are sometimes used to get more nodes in the outer part of the fuel, where temperature gradients are steeper. Steady-state fuel restructuring can change the node sizes. Also, during the transient calculation, the radii will move with the fuel as it expands or contracts due to temperature changes. After the steady-state initialization, the mass of fuel associated with a radial node is constant, at least until fuel-pin disruption and coupling is made to PLUTO2, PINACLE, or LEVITATE.
The inner fuel node is at \(r\ = \ 0\) if there is no central void. Otherwise, it is at the fuel inner surface. The outer fuel node is at the fuel outer surface.
The “structure” represents each pin’s share of the duct wall. A wrapper wire can be lumped in with either the cladding or the structure.
3.2.2.2. Gas Plenum Region¶
The radial mesh structure used in the gas plenum region is shown in Figure 3.2.5. The plenum gas is represented by a single axial and radial node. This gas is in contact with a number of axial cladding nodes. At each axial node, there is one radial node in the cladding, one in the coolant, and two in the structure.
3.2.2.3. Reflector Regions¶
The radial mesh structure in an axial node in a reflector region is shown in Figure 3.2.6. Two nodes are used in the reflector, one in the coolant, and two in the structure.
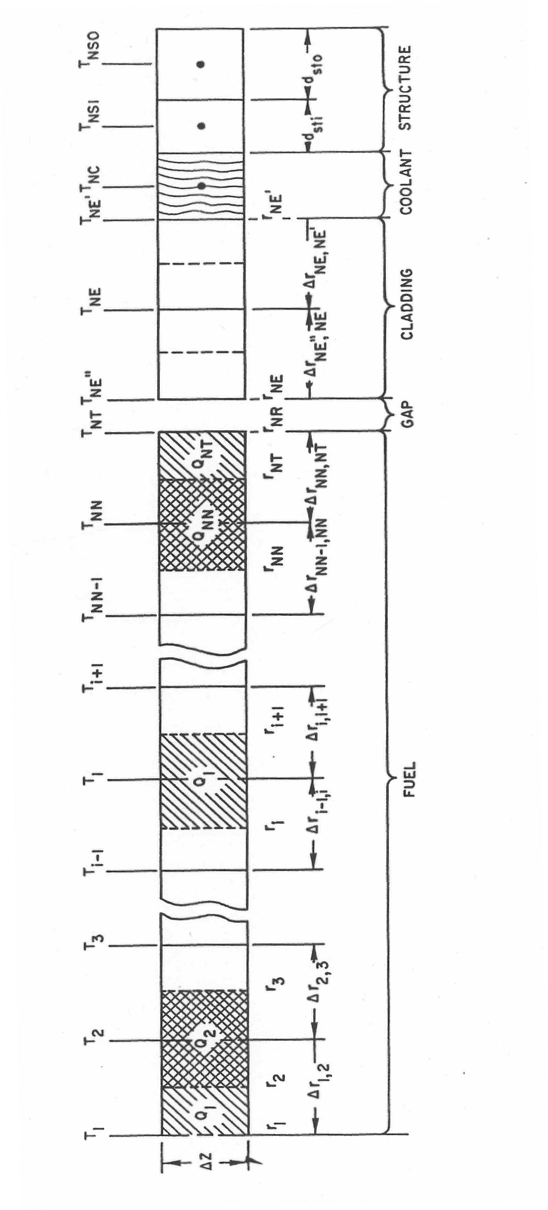
Figure 3.2.4 Radial Temperature Nodes, Core and Axial Blanket Regions¶
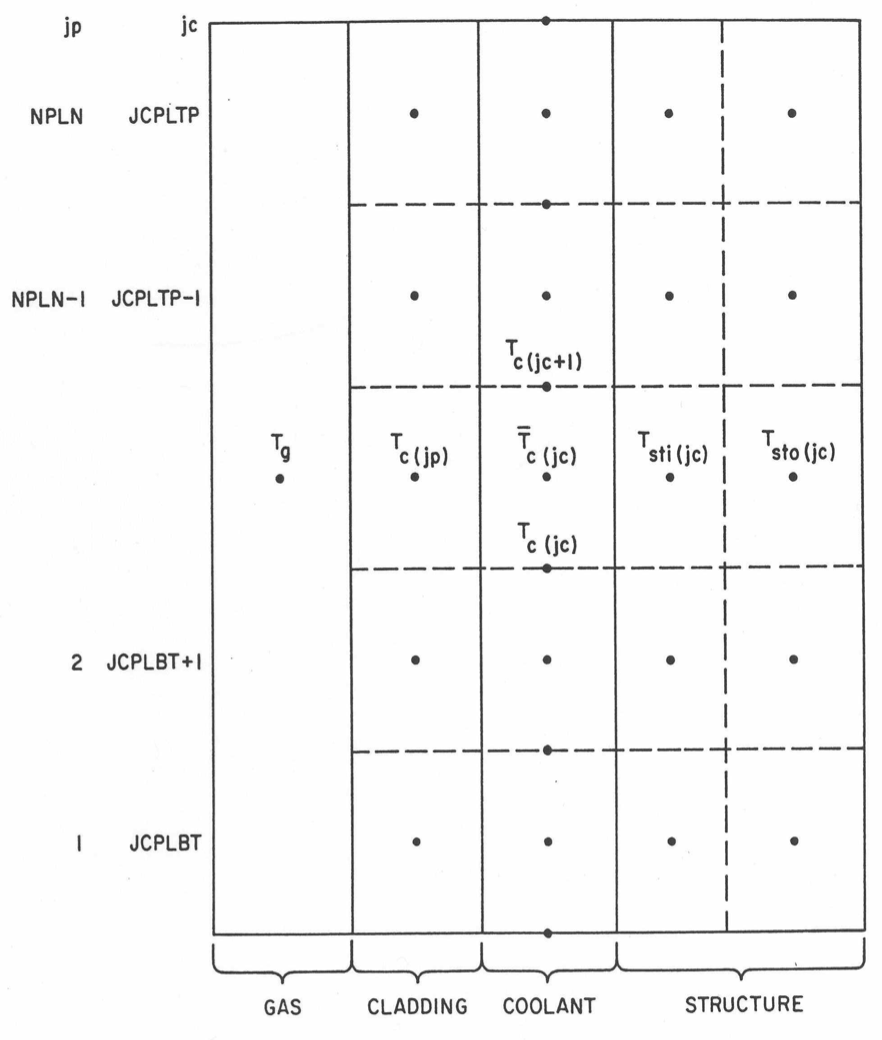
Figure 3.2.5 Radial Temperature Nodes, Gas Plenum Region¶
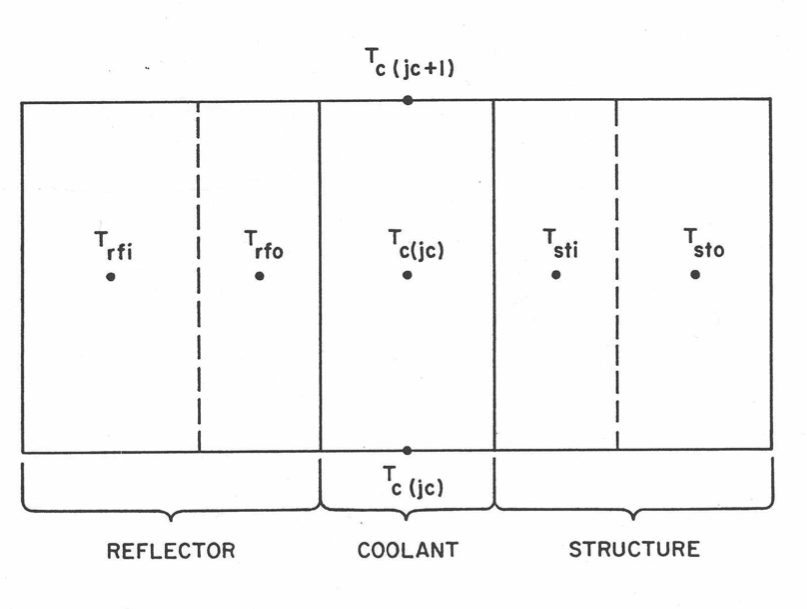
Figure 3.2.6 Radial Temperature Nodes, Reflector Region¶