8.1. Overview and General Background¶
8.1.1. Objectives, General Background, and General Physical Description¶
The response of LMFBR fuel pins to transient accident conditions is an important safety concern. For transients leading to pin failure, the failure modes and initial fuel disruption depend in part on pre‑transient irradiation effects, such as restructuring, fission‑gas retention, fuel‑cladding gap, central void size and makeup. As the transient fuel‑pin models develop, an increasingly rigorous pre‑transient fuel‑pin characterization of the fuel pin is also required. For this reason, an effort has been made to integrate a detailed treatment of the pre‑transient fuel‑pin characterization into SAS4A. At the same time, an attempt has been made to assure that the models are consistent with the transient calculation and, where possible, to develop models in such a manner that they can be used in both the pre‑transient and transient calculations.
Because the phenomena affecting fuel‑pin integrity are not all well understood, most performance codes use one of two methods to predict the pin characterization: (1) empirical correlations derived from a data base of experimentally determined information, or (2) a phenomenological description of the process that contains parameters that need to be calibrated to experiments or the information data base. Care must be exercised with both approaches, but especially with the former method, because unrealistic values can be obtained if the pin conditions fall outside the correlation database. In the phenomenological (or mechanistic) approach the attempt is made to model the physical process taking place and then calibrate this to available data. Since the model attempts to describe the physical processes, it is possible to extrapolate the response to conditions outside the calibration data base with greater assurance than with the correlation approach. It was, therefore, decided that this mechanistic approach would be adopted wherever possible in the DEFORM‑4 module of SAS4A.
This approach is different from that used by earlier versions of the SAS codes [8‑1 ‑ 8‑4]. The former versions contained a very brief steady‑state calculation of one time step at constant power and used correlations to determine the parameters necessary to start the transient calculation. The DEFORM‑4 module simulates the pre‑transient irradiation with a series of power changes and power levels of various time lengths. This provides the means to account for the reactor operating history and its effect on the physical state of the fuel pin, and leads to a more realistic description of the fuel pins subjected to the transient.
The pin is divided into a number of axial segments (≤24) of arbitrary length. If either the PLUTO2 or LEVITATE failed pin modeling is used, then there will be restrictions on the “arbitrariness” of these lengths (see Chapter 14 and Chapter 16). The fuel and cladding are assumed to occupy the same axial segment. Figure 8.1.1 shows an example of the axial and radial discretization for a fuel pin with an upper fission‑gas plenum. The DEFORM‑4 module is concerned with the axial region containing the driver fuel, axial blankets, and the fission‑gas plenum. The core region, i.e., driver and axial blanket fuel segments, is shown in Figure 8.1.2. Illustrated are the three fuel-cladding gap conditions considered: (1) no contact between the fuel and cladding, (2) the fuel elastically straining the cladding, and (3) the fuel plastically straining the cladding. Also illustrated is a central cavity that formed in the hotter regions of the driver fuel.
The fuel in an axial segment is divided into a series of radial cells (≤11). The radial cell boundaries may be determined on the basis of equal mass in each, except the inner and outer cells which contain half the mass of a regular cell, or with each cell thickness being equal, again except for the inner and outer cell which have half the nominal thickness (see Figure 8.1.3). The cladding is divided into two radial cells. The relationship between the general SAS4A cell structure and temperature locations and those used in DEFORM‑4 is indicated in Figure 8.1.4. In the fuel region, the temperatures used by some DEFORM‑4 calculations (refer to the specific models described below) are obtained by averaging the two SAS4A temperatures on either side of the radial cell boundary. Where the property being considered is an average over the annular cell, such as porosity, modulus of elasticity, conductivity, etc., the actual temperatures calculated by the thermal models in SAS4A are used.
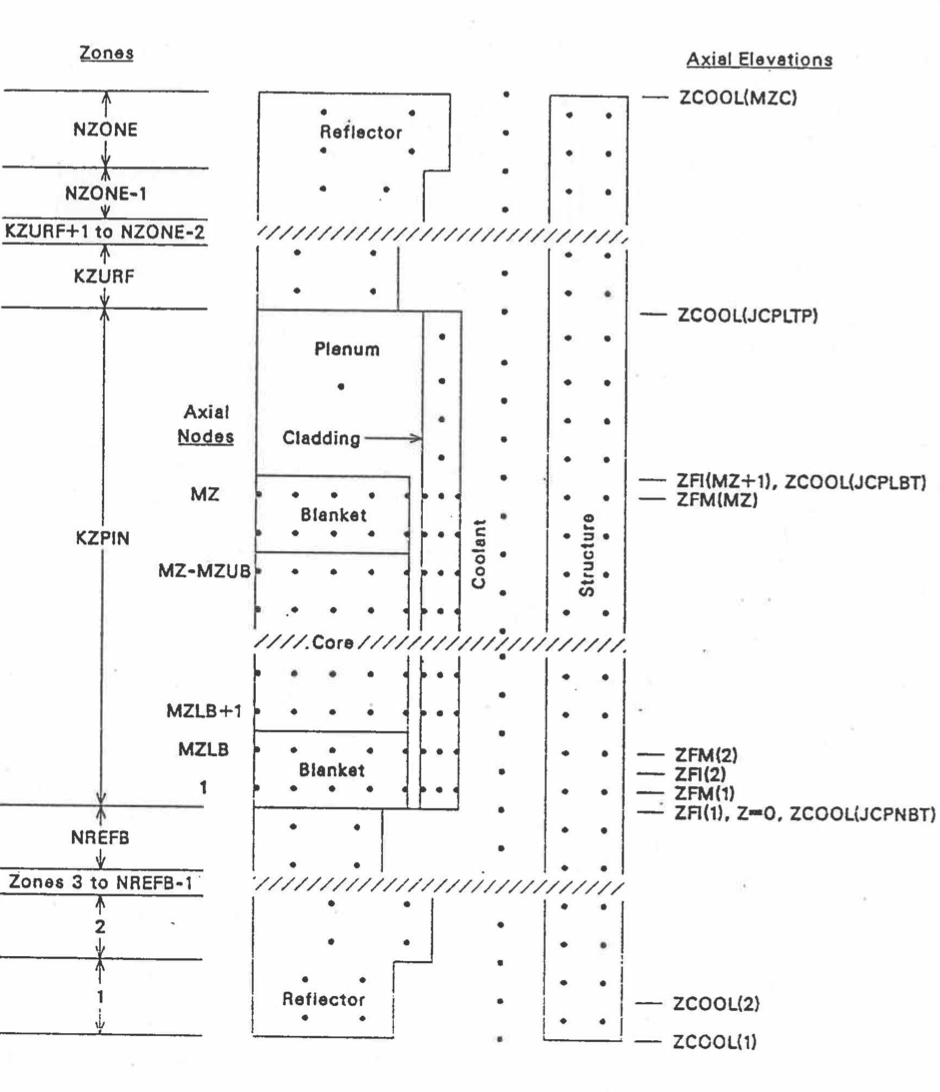
Figure 8.1.1 Schematic of SAS4A Channel Discretization¶

Figure 8.1.2 DEFORM-4 Axial Segmentation with Possible Fuel-cladding Interactions¶
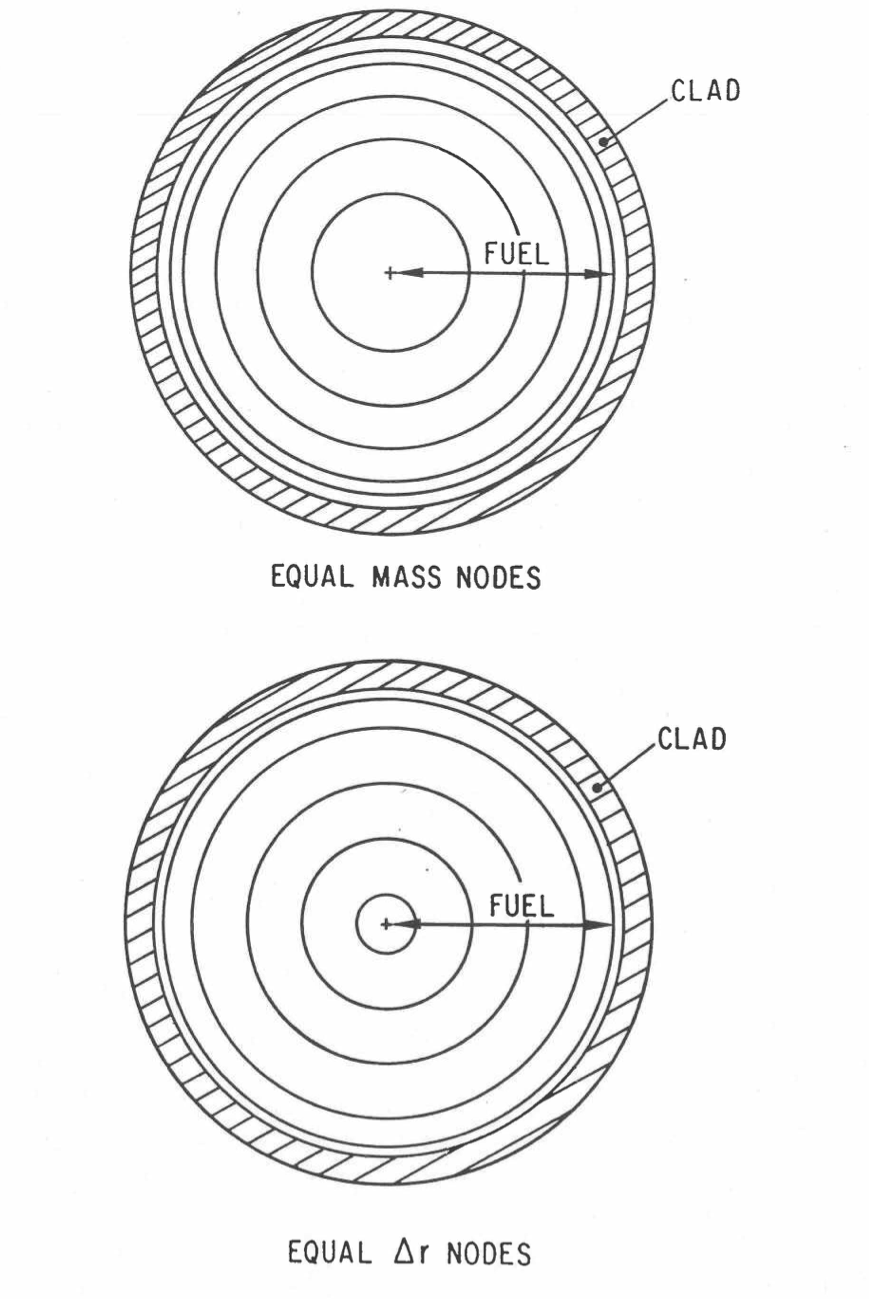
Figure 8.1.3 Radial Cell Construction Options¶
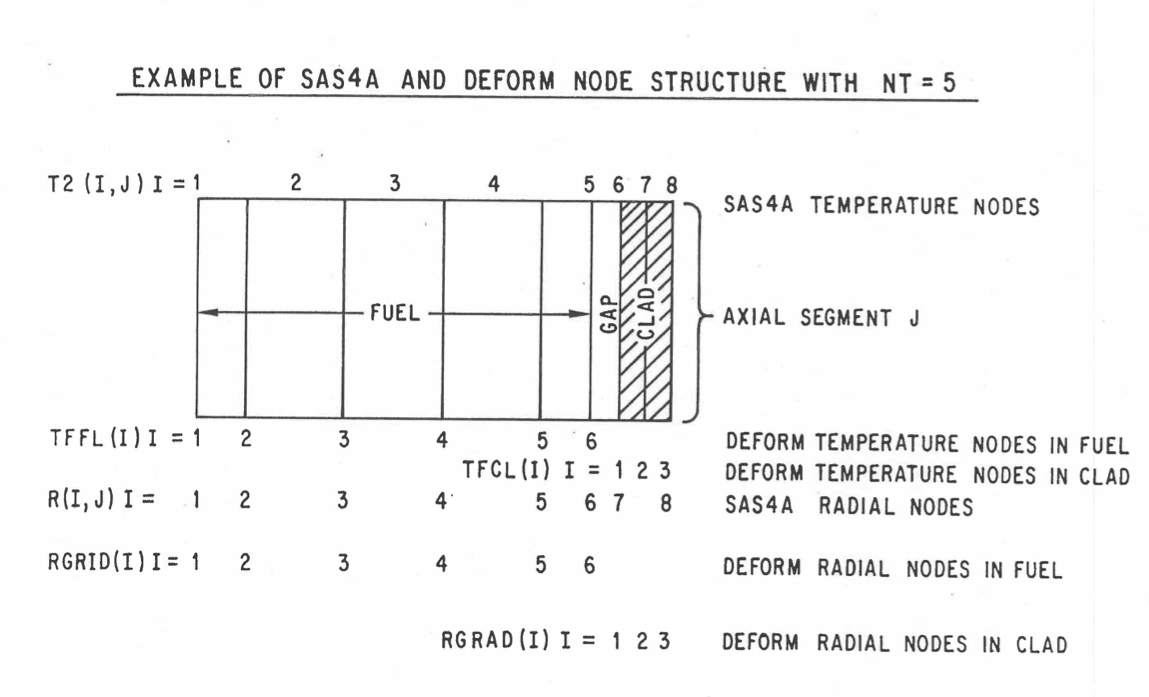
Figure 8.1.4 Relationship Between SAS4A and DEFORM-4 Cells and Cell-boundaries¶
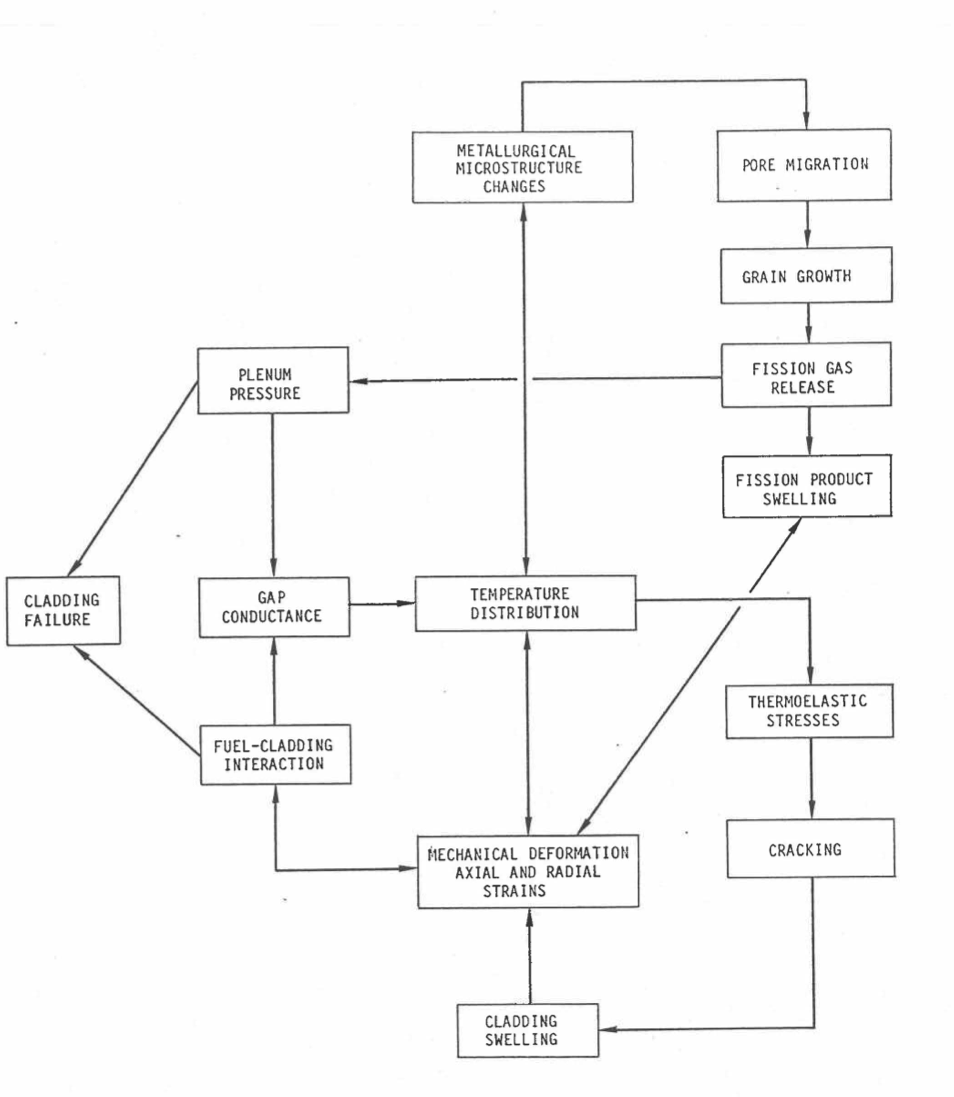
Figure 8.1.5 DEFORM‑4 Mechanical and Phenomenological Considerations and Their Interactions¶
A number of phenomena are treated in the pre‑transient irradiation calculation. These are shown in Figure 8.1.5. Detailed descriptions are given in the following sections, but a brief outline is presented here. These major models include:
As‑fabricated porosity migration by vapor transport (Section 8.3.1), which is responsible for the formation of the central void and provides a radial distribution of the remaining as‑fabricated porosity that affects thermal conductivity;
Grain growth (Section 8.3.2), which affects the fission‑gas release and fuel creep characteristics;
Fission‑gas release (Section 8.3.3), which affects the radial distribution of total porosity and fission‑gas‑bubble‑induced fuel swelling;
Fission‑product swelling (Section 8.3.4), which includes solid fission product and fission‑gas bubble swelling, and affects the radial porosity profile and fuel dimensions; and
Irradiation‑induced cladding swelling (Section 8.3.5), which affects the cladding dimensions and density.
Since the transient calculation covers seconds and minutes rather than days and years, as in the pre‑transient irradiation, the phenomena listed above are not considered, except for the fission‑product swelling. Transient fission‑gas release is assumed to occur only on fuel melting and is treated in the molten cavity routine, Section 8.3.7.
The thermoelastic mechanical calculations for the fuel and cladding are identical in both the pre‑transient and transient. The cladding is treated as an elastic‑perfectly‑plastic material, although one of the options for the flow stress is dependent on strain and strain rate, and this introduces a type of work‑hardening effect. In addition, the cladding is allowed to plasticly creep in response to temperature and stress conditions. Axial and radial deformations result from thermal expansion and mechanical interactions. The effects of fuel‑cladding interaction are also considered in the fission product swelling calculation.
The fuel is allowed to crack radially whenever the circumferential stress exceeds the temperature‑dependent fracture strength. The crack volume varies due to thermal and swelling effects. In the transient, the volume associated with the cracks, the fission gas, and the remaining as‑fabricated porosity can be important in accommodating the thermal expansion on melting and determining the molten cavity pressure.
Fuel‑pin failure can be initiated by a number of criteria. These include the following;
Time,
Fuel temperature,
Melt fraction,
Molten cavity pressure,
Cladding stress,
Eutectic penetration for U-5FS fuel,
Cladding reaching conditions equivalent to PLUTO2/LEVITATE failure propagation model,
Eutectic penetration with cladding stress for metal fuel gauge,
Melt fraction for time and failure propagation for location.
Also included are a number of life‑fraction correlations based on Larson-Miller and Dorn parameters, but these have not been tied into the automatic failure initiation. The use of these to initiate failure is through observation of the life fractions and then selection of a time and location to be used in a subsequent restart calculation.
8.1.2. Interaction with other SAS4A Models¶
Because the DEFORM‑4 module performs all the fuel‑pin characterization and mechanics calculations for SAS4A, it must be capable of exchanging data with the rest of the code. This is done through the use of COMMON blocks accessible by other modules. In the pre‑transient and pre‑failure transient calculations, DEFORM‑4 communicates with the thermal hydraulic models in SAS4A and PINACLE. Once failure has occurred and CLAP, PLUTO2, or LEVITATE become activated, DEFORM‑4 is no longer used for that channel, but still performs the calculations for any remaining unfailed channels.
In the initiation of CLAP, LEVITATE, or PLUTO2, the main responsibility of DEFORM‑4 is to assure that the necessary information is available for these modules to continue the calculation. If the user has so specified by appropriate input options, then DEFORM‑4 will determine when the failure has occurred and initiate the activation of the appropriate module for fuel motion. If it is not being used, failure can still be initiated, but important parameters, such as fission gas distributions and molten cavity pressures, will not be available for PLUTO2 and LEVITATE. This will cause significant problems in the computations carried out by these modules. The CLAP module does not depend on DEFORM‑4 results in its calculations for cladding motion, except for the initial pin dimensions.
The main communication with the rest of SAS4A on an interactive basis is through the core temperatures and pressures supplied by the thermal hydraulic models and then the radii, axial lengths, porosity distributions which affect thermal conductivities, and gap conductances which are returned from DEFORM‑4. In order to avoid time‑consuming iterations between the thermal hydraulic models and DEFORM‑4, the calculations are performed serially. The thermal hydraulic models use the geometry they have at the beginning of a time step with the power, flow, and time‑step length to determine temperatures at the end of the time step (see Chapter 3). These final temperatures and the initial temperatures are then used by DEFORM‑4 to determine the thermal mechanical changes that take place during the same interval. The new conditions are then transferred back to the thermal hydraulic routines as the initial conditions for the next time step.
This method of interaction with the SAS4A thermal hydraulic models has been employed to avoid the resource‑consuming iterations that could occur between the thermal hydraulic and pin characterization routines. These iterations would assure complete consistency between the temperatures and the characterization state of the pin, but at a price in computational effort that would preclude the use of the code for many of the multiple channel, extended pre‑transient and transient cases of interest in initiating‑phase accident analysis. Instead of iterations, there is control over the length of the computational time step. In the early pre‑transient irradiation where pore migration and initial fission‑gas release cause changes in the geometry and heat‑transfer properties that would greatly affect the temperatures, time intervals on the order of one to two days should be used. During power changes it may be necessary to cut these further, especially during the initial startup to full power. In later stages, the time steps can be on the order of 10 to 30 days. During the transient where the time steps are controlled by a variety of restrictions, such as maximum reactivity change, maximum temperature change, etc., the heat‑transfer time steps are small enough, on the order of less than a second, to remove any problems with inconsistencies. DEFORM‑4 would be able to handle considerably longer time steps without problems. In practice, these types of limits have resulted in excellent results with minimum computational effort.