14.8. Description of Input to and Output of the PLUTO2 Module¶
14.8.1. PLUTO2 Input¶
The SAS4A input variables required specifically by the PLUTO2 fuel motion model are given in Table 14.8.1 with their suggested values in MKS units (kilogram, meter, second, degree Kelvin). Also indicated in Table 14.8.1 are some particular sections of the documentation in which the input variables are explained, or some particular equations in which the variables are used. The first column of the table gives the location of the variable in the complete input deck of the SAS4A code. The second and the third columns give the Fortran variable names used in the code and the SAS4A input description, and the corresponding symbols, if any, used in the mathematical equations in the documentation.
14.8.2. PLUTO2 Output¶
The main PLUTO2 output (see Figure 14.8.1) for a given SAS4A channel (the channel number is shown at the top of each output page) is separated into two major sections. One of these sections (output items 1 to 7 in Figure 14.8.1) deals with the in-pin motion and the fuel and fission-gas ejection from the pins and the other section (output items 8 to 18 in Figure 14.8.1) deals with the motion of fuel, sodium, and fission gas in the coolant channels. All output is strictly in SI units (e.g., kg, m, s, K, joules, pascals, etc.). At the time of entry to PLUTO2 module, the variables of output item 18 are printed with the message “PLUTO STARTS” and then follow output items 1 to 18.
SAS4A Input Location |
Fortran Variable |
Symbol |
Describing Section |
Equation Number |
Suggested Value in MKS Units |
Comments |
---|---|---|---|---|---|---|
Block 1, INPCOM |
||||||
37 |
KFAILP |
0 |
Mechanistic axial propagation of pin failure is opted. |
|||
38 |
NCPLEV |
3 |
The fuel motion calculation is switched from PLUTO2 to LEVITATE when 3 axial cladding nodes have exceeded the cladding liquidus temperature. |
|||
Block 13, PMATCM |
||||||
1124 |
RGAS |
130.637 |
||||
1125 |
CINAFO |
For a consistent input, the coolant film volume fraction (CINAFO) should be evaluated from cladding and structure film thicknesses WFO and WFSOO of channel 1. If CINAFO so evaluated for another channel disagrees with the above value, a consistent input is not possible. |
||||
1126 |
CIBBIN |
0.7 |
See Section 14.4.3.1. |
|||
1127 |
CIREFU |
2100.0 |
||||
1128 |
CIFRFU |
0.02 |
Page 264 of Ref. [14-49]. |
|||
1129 |
CIFUMO |
0.5 |
All intra-pin axial momentum of the fuel perhaps will not be retained after ejection into coolant channel. |
|||
1130 |
CIVOID |
0.5 |
See Section 14.4.3.4.1.1. |
|||
1131 |
CIA1 |
1.0 |
A recent theoretical evaluation [14-51] gives CIA1 = 3.3 to 5.0 but a preliminary calibration of the PLUTO2 module in the SAS4A version 1.0 has been done with CIA1 = 1.0 |
|||
1132 |
CIA2 |
2.0 |
See Section 14.4.3.4.2.1. |
|||
1133 |
CIA3 |
0.0158 |
This value is good for mixed oxide fuel but not for metal alloy fuel |
|||
1134 |
CIA4 |
0.6 |
CIA4 should e larger than CIVOID. |
|||
1135 |
CIA5 |
-1.7 |
Ref. [14.49, 14-63]. |
|||
1136 |
CIA6 |
0.4272 |
||||
1139 |
CPFU |
\(C_{\text{p,fu}}\) |
500.0 |
Ref. [14-59]. |
||
1140 |
CDFU |
\(k_{\text{fu}}\) |
3.0 |
Ref [14-60]. |
||
1141 |
CMNL |
\(K_{\text{Nf}}\) |
4.6D-10 |
The compressibility of liquid sodium is very temperature-dependent and this value [14-60] corresponds to 1200 K, roughly the sodium temperature in the vicinity of pin failure at the time of failure. |
||
1142 |
CDNL |
\(K_{\text{Nl}}\) |
50.0 |
This is liquid sodium thermal conductivity at about 1200 K [14-59]. |
||
1143 |
CIETFU |
0.1 |
||||
1144 |
CDVG |
\(k_{\text{vg}}\) |
0.067 |
The thermal conductivity of a gas mixture is very dependent on its temperature and composition. This value of CDVG is sodium vapor thermal conductivity at 1500 K [14-61], roughly 300 K higher than the assumed sodium temperature in the vicinity of pin failure at the time of failure. |
||
1145 |
VIFI |
9.5D-5 |
This is xenon viscosity at about 1500 K extrapolated from temperature-dependent measured data [14-62] by fitting an equation of the form T0.89 (T = xenon temperature). It is not yet used in the code. |
|||
1146 |
CFNACN |
6.0D4 |
||||
1147 |
CFNAEV |
6.0D5 |
||||
1148 |
FIFNGB |
0.1 |
Also see suggested values of DEF”ORM input in Chapter 8. |
|||
1149 |
VINL |
\(\mu_{\text{Nl}}\) |
1.5D-4 |
This is liquid sodium viscosity at about 1200 K [14-61]. |
||
1150 |
VIVG |
\(\mu_{\text{vg}}\) |
2.2D-5 |
This viscosity of a gas mixture is very dependent on its temperature and composition. This value of VIVG is sodium vapor viscosity at about 1500 K [14-61]. |
||
1151 |
EGFUSO |
\(e_{\text{fu,sol}}\) |
1.0D6 |
Ref. [14-59]. |
||
1152 |
DZPLIN |
0.02 |
DXPLIN must be smaller than the shortest axial mesh cell in channel. |
|||
1153 |
CFCOFV |
6.0D4 |
This parameter is not yet used in the code. |
|||
1155 |
C1VIPR |
3.0D-3 |
||||
1156 |
C2VIPR |
0.0 |
||||
1157 |
SUFU |
\(\sigma_{\text{fu}}\) |
0.45 |
For a consistent input, this value should equal the value input in |
||
1158 |
RAFPLA |
2.5D-4 |
||||
1159 |
RAFPSM |
2.5D-4 |
||||
1160 |
VFNALQ |
0.33 |
See Section 14.4.3.1. |
|||
1161 |
EGBBLY |
EGFUSO + UFMELT(1)*0.5 |
Fuel freezing is initiated when the fuel internal energy drops below the energy corresponding to 0.5 melt fraction. The value of the latter energy should be evaluated by adding 0.5 of the latent heat of fusion of fuel type 1 ( |
|||
1162 |
VIFULQ |
\(\mu_{\text{fu,liq}}\) |
4.3D-3 |
Ref. [14-59]. |
||
1163 |
VFNARE |
0.8 |
VFNARE > VFNALQ |
|||
1164 |
DTPLIN |
\(\Delta t_{\text{PL}}\) |
2.5D-5 |
|||
1165 |
AXMX |
1.0 |
Although the results of the code (except the volume fractions) are independent of the value of AXMS, the volume fractions are meaningful if AXMX is set equal to the cross-sectional if AXMS is set equal to the cross-sectional area within the outer surface of the subassembly hexcan. |
|||
1166 |
EPCH |
1.0 |
||||
1167 |
TIPLMX |
(last paragraph) |
1.5 |
|||
1168 |
DTPLP |
2.0D-3 |
||||
1169 |
FNMELT |
0.9 |
||||
1170 |
CIRTFS |
16.67 |
||||
1172 |
CIFUFZ |
1.0 |
It is not yet used in the code. |
|||
1173 |
TIFP |
0.015 |
It makes no difference if both fuel particle radii are equal. |
|||
1174 |
CIANIN |
0.5 |
||||
1175 |
TEFAIL |
TESOL(1) |
It should be set equal to the solidus temperature of cladding type 1 (location 810). |
|||
1176 |
FNARME |
0.9 |
||||
1177 |
PRFAIL |
0.0 |
||||
1178 |
EGMN |
EGFUSO + UFMELT(1)*0.3 |
EGMN should be smaller than EGBBLY. It is assumed that continuous fuel flow regimes cannot be initiated below the energy corresponding to 0.3 melt fraction. |
|||
1179 |
HCFFMI |
1.0D5 |
||||
1180 |
HCFUBB |
3.0D4 |
||||
1181 |
FNHTFU |
0.1 |
It is not yet used in the code. |
|||
1184 |
TECLMN |
TESOL(1) |
The value should be chosen equal to the solidus temperature of cladding type 1 ( |
|||
1185 |
TECLRL |
TELIQ(1) |
See Section 14.4.3.2. |
|||
1186 |
CIHCFU |
0.0158 |
See location 1133. |
|||
1187 |
HCCLMI |
1.0D5 |
||||
1188 |
CMFU |
\(K_{\text{fu,liq}}\) |
6.0D-11 |
The compressibility of liquid mixed oxide fuel is very dependent on temperature and the chosen value is for fuel at 4000 K [14-60]. |
||
1195 |
CDCL |
32.0 |
This value is solid cladding thermal conductivity averaged over the temperature range 1200 K to the cladding solidus temperature of 1700 K [14-59]. |
|||
1196 |
CPCL |
\(C_{\text{p}}\) |
655.0 |
This value is the cladding specific heat averaged over the temperature range 1200 K to the solidus temperature of 1700 K [14-59]. |
||
1197 |
CPCLRH |
\(\rho_{\text{i}} C_{\text{p,i}}\) |
7400*CPCL |
This value is obtained using the cladding specific heat CPCL (location 1196) and a cladding density of 74000 kg/m3 averaged over the range 1200 K to the solidus temperature of 1700 K [14-59]. |
||
1198 |
RHSLBT |
\(\rho_{\text{Nl},\text{ls}}\) |
728.0 |
This is liquid sodium density at about 1200 K [14-61]. |
||
1199 |
RHSLTP |
\(\rho_{\text{Nl},\text{us}}\) |
0.975 * RHSLBT |
It is assumed that the temperature difference between the upper and lower liquid coolant slugs is about half of the coolant temperature rise in core (ΔTcore), and the corresponding density difference is 2.5% for (ΔTcore) of about 150K. The effect of the transient heat-up of the coolant on this estimate of the input has been ignored. |
||
1201 |
COEFDL(2) |
9.3D-5 |
Ref. [14-59]. |
|||
1210 |
EGSESO |
0.834D6 |
Ref. [14-59]. |
|||
1211 |
EGSELQ |
EGSESO + UEMELT(1) |
This value is obtained by adding the latent heat of fusion of cladding type 1 (location 816) to the solidus internal energy. |
|||
1212 |
CPSE |
774.0 |
This is the constant value of the cladding specific heat at temperatures above the liquidus [14-59]. |
|||
1214 |
FNSROS |
0.2 |
The structure thickness should be divided into two mesh intervals such that the mesh interval contacting the coolant has a thickness equal to 20% of the total thickness. For consistency, this parameter must be in agreement with the input structure mesh thicknesses in |
|||
1231 |
SRFMLE |
1.0 |
Also see LEVITATE input description in Chapter 16. |
|||
Block 51, INPCHN |
||||||
71 |
NRPI1 |
NPIN |
All pins are assumed to fail when the fuel pin failure criterion is satisfied. |
|||
74 |
IPSIZE |
1 |
||||
75 |
IBUGPL |
0 |
||||
76 |
ICFINE |
0 |
||||
77 |
IPRINT |
0 |
||||
78 |
IPLOT |
2 |
||||
79 |
IBGO |
0 |
||||
80 |
IBSTOP |
0 |
||||
81 |
IBNEW |
0 |
||||
82 |
IPGO |
0 |
||||
83 |
IPSTOP |
2000 |
||||
84 |
IPNEW |
20 |
||||
Block 65, FUELIN |
||||||
2 |
FMELTM |
0.2 |
This is required for the in-pin flow calculation of molten fuel. |
|||
19 |
PFFAIL |
0.0 |
This value of PCFAIL implies that the DEFORM-IV computed molten fuel cavity pressure at pin failure time will be used in the PLUTO2 calculation. |
The PLUTO2 variables that are printed in output items 1 and 2 of Figure 14.8.1 are listed below:
ISTEP |
Current main (point kinetics) time-step number. |
---|---|
TOTAL TIME |
Time since beginning of transient. This is the regular SAS4A time. |
ICYCLE |
Current PLUTO2 calculational cycle for the SAS4A channel shown at the top for the page; the calculational step for the cycle number shown has just been completed at the time of a printout (see flowchart in Figure 14.7.3). |
TIMEPL |
PLUTO2 time. This is counted from the time of pin failure in this channel. |
DTPLU |
Current PLUTO2 time-step size. |
In output item 3 total masses per subassembly are shown: |
|
SMFUPI |
Current total mass of fuel in all failed pins of one subassembly. |
SMFUST |
Current total stationary (unmelted) fuel mass in all failed pins of one subassembly. |
SMFUCA |
Current total molten fuel mass in the pin cavities of all failed pins of one subassembly. |
SMFICA |
Current total free fission-gas mass in the pin cavities of all failed pins of one subassembly. |
SMFSCA |
Current total dissolved fission-gas mass in the cavities of all failed pins. |
In output item 4, various other total masses for one subassembly are displayed: |
|
SMFUME |
Total mass of fuel which has melted into the molten pin cavities of all failed pins in one subassembly since the time of pin failure. |
SMFIME |
Total mass of the free fission gas having been added to the cavities of all failed pins in one subassembly since the time of pin failure; the total mass of dissolved fission gas having been added t the pin cavities can be calculated by multiplying SMFIME by (1-FNFIGB)/FNFIGB where FNFIGB is the input fraction of fission gas on the grain boundaries of solid fuel. |
SMFSRT |
Total mass of free fission gas that has been generated due to coalescence of the small (dissolved) fission-gas bubbles in all the cavities of the failed pins of one subassembly. |
SMFUEJ |
Total mass of fuel that has been ejected into the coolant channels since pin failure. The sum of SMFUEJ and SMFUPI should always give the total initial fuel mass of the failed pins in the subassembly considered. |
SMFIEJ |
Total free fission-gas mass ejected from all failed pins per subassembly. |
In output item 5, several columns showing various quantities per single pin node of failure group 1 are printed: |
|
K |
Axial cell index of the pin grid; only cells which cover the molten cavity are shown. The pin gird actually extends from the bottom of the lower blanket to the top of the upper blanket. |
IDISR |
Gives information about cladding disruption and fuel and gas ejection. IF IDISR = 0, cladding is not ruptured; if IDISR = 2, cladding has ruptured but currently there is no ejection; if IDIST = 3, cladding has ruptured and fuel and gas ejections are going on. |
DICA |
Current diameter of the molten cavity in pin cell K. |
AREAFR |
Current are fraction of the molten pin cavity in pin cell K (i.e., cavity cross section/total fuel cross section). |
FUSTAT |
Stationary (solid) fuel mass in cell K. Stationary core fuel masses above and below the cavity are shown in output item 16. |
FUELM |
Mobile (cavity) fuel mass in cell K. |
FUELSD |
Fuel smear density in the cavity. |
RHFUCA |
Theoretical fuel density in the cavity, the fuel volume fraction in the cavity is the ratio of FUELSD to RHFUCA. |
FISGM |
Free fission-gas mass in the cavity part of cell K. |
FISGDM |
Dissolved fission-gas mass in the cavity part of cell K. |
FNFIGB |
Fraction of fission gas on the grain boundaries of the melting-in fuel; this fraction is instantaneously becoming free fission gas upon melt-in; it is presently a single input value. |
FUEJ |
Fuel mass ejected from pin cell K during the current time step. |
FIEJ |
Free fission-gas mass ejected from pin cell K during the current time step. |
Output item 6 also prints several columns displaying variables pertaining to the in-pin motion: |
|
K |
Axial cell index of the pin grid. |
I |
Axial index of the corresponding channel cell. |
ZZPI |
Axial location of the lower cell boundary in the pin cavity. |
UFPI |
Fuel/fission-gas mixture velocity at the lower cell boundary. All other pin cavity quantities shown are at the cell centers. |
PRCA |
Total physical pressure in-cavity cell K. |
PRFVPI |
Fuel vapor pressure component that is based on the average fuel temperature in cavity cell K. |
PRVI |
Artificial viscous pressure for damping numerical oscillations behind shock fronts. |
EGFUCA |
Average internal fuel energy in cavity cell K. |
TEFUCA |
Average fuel temperature in cavity cell K. |
FUMESM |
Mass of fuel that has molten into cavity cell K during the current time step. |
FIMESM |
Mass of free fission gas that has been added to cell K during the current time step due to fuel melt-in. |
SIGCL |
Cladding hoop stress for cell K; a negative value indicates that the channel pressure is higher than the cavity pressure. A value of zero indicates that the cladding in this cell has failed. |
UTS |
Ultimate tensile strength of the cladding material at temperature TECLIN (see output item 15). |
Output item 7 shows the sum of the fuel and sodium voiding reactivities and also these two reactivities separately. These reactivities are for the entire SAS4A channel under consideration which usually contains more than one subassembly (see input quantity NSUBAS). For multi-channel runs the same fuel and sodium voiding reactivities are also printed out in the short reactivity printout which appears at the end of each main (point kinetics) time step. |
|
Output item 8 is the first row describing coolant channel variables; it prints several important integer quantities in the coolant channels (see also Figure 14.1.4): |
|
IFMIBT |
Bottom cell of the interaction region (i.e., the region between the upper and lower sodium slugs). |
IFMITP |
Top cell of the interaction region. |
IFFUBT |
Bottom cell of the fuel region. |
IFFUTP |
Top cell of the fuel region. |
IFFIBT |
Bottom cell of fission-gas region. |
IFFITP |
Top cell of fission-gas region. |
IFFVBT |
Bottom cell of fuel vapor region. |
IFFVTP |
Top cell of fuel vapor region. |
IFRIBT |
Lowest cell containing a cladding rupture. |
IFRITP |
Highest cell containing a cladding rupture. |
PRIN |
Current inlet pressure. |
PREX |
Current outlet pressure. |
Output item 9 shows total fuel and sodium masses in the interaction region and the fuel and sodium masses which have been ejected out of the top of the subassembly: |
|
TOFUMA |
Total fuel mass in the coolant channels of one subassembly; this should be equal to SMFUEJ (see output item4) until fuel gets ejected out of the top of the subassembly. |
FUMATP |
Fuel mass ejected out of the top of one subassembly. |
TONAMA |
Total sodium mass in the interaction region of one subassembly. |
TPNAMA |
Sodium mass ejected out of the top of one subassembly. |
Output item 10 shows total fission-gas masses: |
|
TOFIMA |
Total mass of free fission-gas in the interaction region of one subassembly. |
TODGCH |
Total dissolved fission-gas mass in the interaction region of one subassembly. |
TODGCL |
Total dissolved fission-gas mass in the plated-out fuel on the cladding and structure (this is included in TODGCH discussed above). |
FIMATP |
Total free and dissolved gas masses ejected out of the top of one subassembly. |
Output item 11 also shows total fission-gas masses per subassembly: |
|
TOFIDG |
Total free and dissolved fission-gas masses in all subchannels and in all failed pins of one subassembly. |
TODG |
Total dissolved fission-gas in all subchannels and in the cavities of all failed pins of one subassembly. |
TOFI |
Total free fission gas in the cavities of all failed pins and in all subchannels of one subassembly. |
TOFIST |
Total fission-gas mass in the stationary (unmelted) fuel of all failed pins in a subassembly (only one type of gas is currently treated in the solid part of the fuel pins in SAS4A). |
Output item 12 shows channel interface locations and velocities of the various component regions (see Figure 14.1.4 in Section 14.1): |
|
SLIFBT(1) |
Location of the upper slug interface of the lower coolant slug, which is also the location of the lower interaction zone boundary. |
SLIFBR(2) |
Velocity of the upper slug interface of the lower coolant slug. |
SLIFTP(1) |
Location of the lower slug interface of the upper coolant slug. |
SLIFTP(2) |
Velocity of the lower slug interface of the upper coolant slug. |
FUIFBT(1) |
Location of the lower boundary of the region containing fuel. |
FUIFBT(2) |
Velocity of the lower boundary of the region containing fuel. |
FUIFTP(1) |
Location of the upper boundary of the region containing fuel. |
FUIFTP(2) |
Velocity of the upper boundary of the region containing fuel. |
FIIFBT(1) |
Location of the lower boundary of the region containing free fission gas. |
FIIFTP(1) |
Location of the upper boundary of the region containing free fission gas. |
Output item 13 shows several columns of variables pertaining to individual channels cells: |
|
I |
Axial channel index. |
K |
Index of pin cavity cell which is at the same elevation as channel cell I. |
ZC |
Location of the lower boundary of cell I. |
UMCH |
Velocity of the mixture of liquid sodium, sodium vapor, free fission gas and fuel vapor at the lower boundary of cell I (i.e., at ZC). |
UFCH |
Velocity of the liquid or solid fuel at the lower boundary of cell I (i.e., at ZC). |
PRCH |
Total pressure in cell I. |
PRNV |
Sodium vapor pressure which can be:
|
PRFI |
Free fission-gas pressure. This pressure component is equal to the total pressure for a sodium single-liquid-phase pressure situation. |
PFFV |
Fuel vapor pressure. |
THCHOP |
Open channel cross-sectional area per subassembly divided by reference area AXMS which is input. The open channel cross-sectional area is the total channel cross-section area minus the cross-sectional area of the frozen fuel crusts. THCHOP can also be interpreted as the open channel volume fraction. |
THNAFM |
Liquid sodium film cross-sectional area per subassembly divided by the input reference area AXMX. |
THNL |
Total liquid sodium cross-sectional area per subassembly divided by the input reference area AXMX. |
Output item 14 contains the other area fractions and also the total component masses per axial cell I: |
|
I |
Axial channel index. |
IFLAG |
Indicates the type of fuel flow regime present in cell I. IFLAG = 1 indicates the particulate flow regime, IFLAG = 3 indicates partial or full annular fuel flow, and IFLAG = 4 indicates bubbly fuel flow; |
THFUCH |
Mobile channel fuel cross-sectional area per subassembly divided by the input reference area AXMX. |
THFF |
Stationary fuel crust cross-sectional area per subassembly divided by the input reference area AXMX. |
THVG |
Cross-sectional area of the vapor/gas flow per subassembly divided by input reference area AXMX. |
FUMASS |
Mobile channel fuel mass in channel cell I (a channel cell in PLUTO2 includes all subchannels of a subassembly). |
FUFFMA |
Stationary frozen film mass in channel cell I. |
NAMASS |
Total sodium mass in channel cell I. |
FIMASS |
Total free fission-gas mass in channel cell I. |
FIDGMA |
Mass of fission gas dissolved in the mobile fuel in channel cell I. |
FIFFMA |
Mass of fission gas dissolved in the frozen fuel crusts in channel cell I. |
Output item 15 contains the variable columns giving channel, cladding, and structure temperatures in cell I: |
|
I |
Axial channel index. |
IDISR |
Gives information about cladding disruption and fuel and gas ejection: If IDISR = 0, cladding is not ruptured; if IDISR = 2, cladding is ruptured but currently no ejection going on; if IDISR = 3, cladding is ruptured and fuel and gas ejection are going on; IDISR also appears in output item 5. |
TENA |
Sodium temperature. |
TEFUOS |
Fuel temperature. The fuel temperature will be in the melting range if TFSOL < TEFUOS < TFLIQ (TFSIK and TFLIQ ARE INPUT). The fuel melt fraction in this case is: (TEFUOS - TFSOL)/(TFLIQ - TFSOL); |
TEFFCL |
Temperature of the frozen fuel crust on the cladding. |
TEFFSR |
Temperature of the frozen fuel crust on the structure. |
TECLOS |
Temperature of the cladding outer surface. The outer cladding temperature will be in the melting range if TESOL < TECLOS < TELIQ (TESOL and TELIQ are input). The cladding melt fraction in this case is: (TECLOS - TESOL)/(TELIQ - TESOL); |
TECLIN |
Temperature of the middle cladding node. |
TESROS |
Temperature of the structure surface facing the coolant channel. |
TESRIN |
Temperature of the structure node facing the neighboring subassembly. |
Output items 16 and 17 show the pin and total fuel masses for the entire axial region containing fuel. The fuel-pin masses outside the interaction region were not shown before. The following variables are displayed: |
|
MAFUPI |
Total mass in all fuel-pin cells corresponding to channel cell I (including the stationary fuel in both the failed and unfailed pin nodes and the mobile fuel in the failed pin nodes). |
MAFUTO |
Sum of the total fuel in channel cell I and MAFUPI (see above). This output is valuable for comparing with one-dimensional hodoscope fuel distribution curves. |
Output item 18 contains the variable columns pertaining to the temperature distribution along the entire channel including the regions outside the interaction region: It should be noted that the temperatures outside the interaction region which are shown here are calculated at the end of the last heat-transfer time step which can be fractions of a millisecond before the time of the current printout. |
|
I |
Axial channel index. |
ZCOOL |
Location of the lower boundary of mesh cell I. |
TREFL2(2) |
Inner reflector node temperature. Reflectors can be located only below or above the pin zone K2PIN. |
TREFL2(1) |
Temperature of the outer reflector node which is facing the coolant. |
T1(NEPP) |
Inner cladding surface temperature (i.e., next to the fuel). |
T1(NE) |
Cladding temperature of the middle cladding node. |
T1(NEP) |
Outer cladding surface temperature (i.e., next to the coolant). |
TENA |
Sodium temperature. |
TSAT |
Sodium saturation temperature. This is calculated only for the pin zone to detect sodium-boiling initiation. |
TSTR2(1) |
Temperature of the structure node facing the coolant channel. |
TSTR2(2) |
Temperature of the structure node facing the neighboring hexcan wall. |
PRCH |
Pressure in the coolant channel. This is calculated outside the fuel-pin zone only if the interaction region extends beyond it. |
Output item 18 shows the message “PLUTO ENDS”. This indicates that control is transferred from PLUTO2 to the SAS4A transient driver TSTHRM at the end of a primary-loop time step. The variables printed after the message “PLUTO ENDS” are not labeled in order to save space in multi-channel runs. These variables are: |
|
ICYCLE |
PLUTO2 calculational cycle. |
IFMIBT |
Lowermost interaction zone cell. |
IFMITP |
Uppermost interaction zone cell. |
IFRIBT |
Lowermost channel cell with failed cladding. |
IFRITP |
Uppermost cladding cell with failed cladding. |
IFFUBT |
Lowermost channel cell containing fuel. |
IFFUTP |
Uppermost channel cell containing fuel. |
ICH |
SAS4A calculational channel. |
REA1 |
Sodium voiding reactivity for channel ICH. |
REA2 |
Fuel reactivity for channel ICH. |
TIMEPL |
PLUTO2 time for channel which is counted from the time of pin failure. |
The above 11 variables of output item 18 are also printed with the message “PLUTO STARTS”, in the same order, at the time of entry to the PLUTO2 module, before printing output item 1.
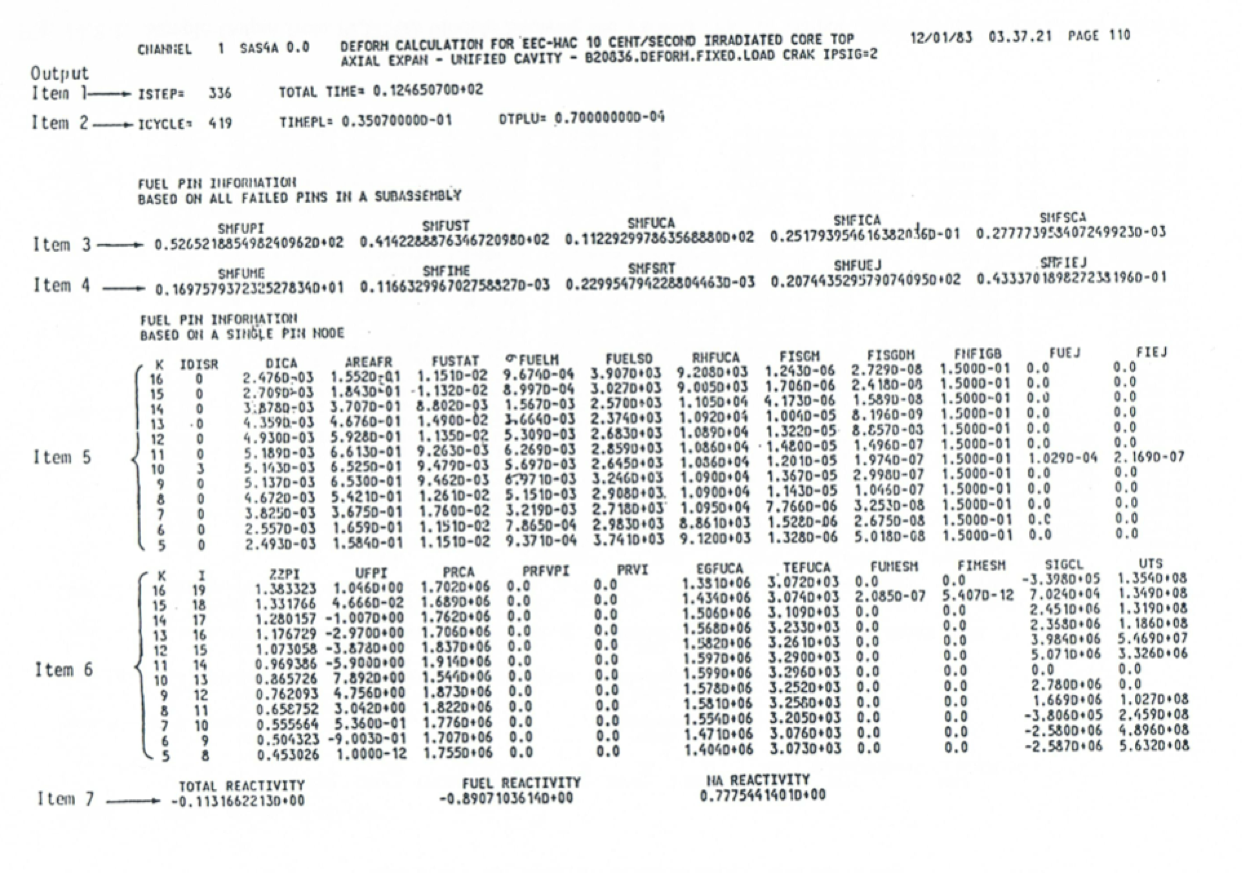
Figure 14.8.1 Sample Output from PLUTO2 Module showing the Various Items of Output Described in Section 14.8.2¶
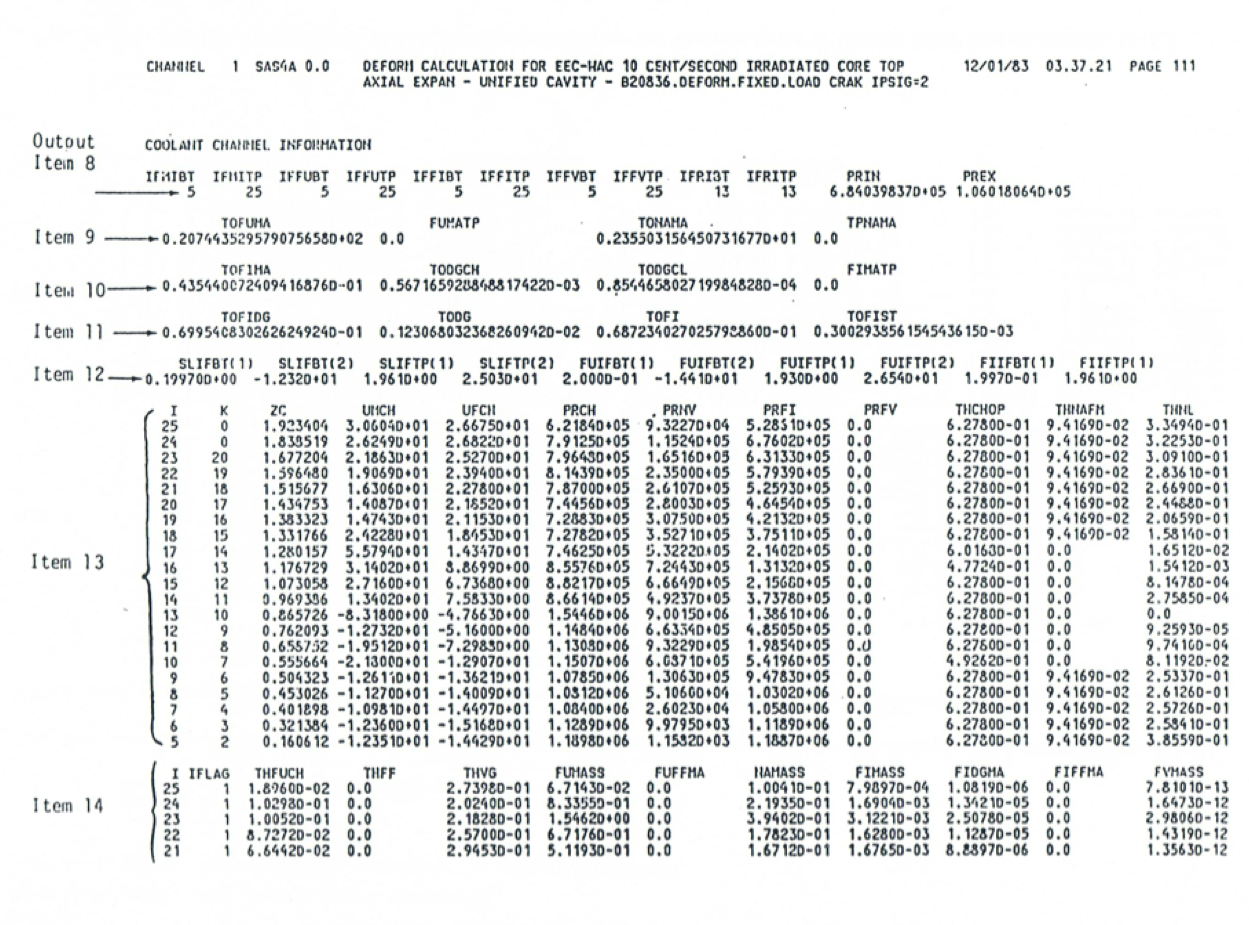
Figure 14.8.2 Sample Output from PLUTO2 Module showing the Various Items of Output Described in Section 14.8.2 (Cont’d)¶
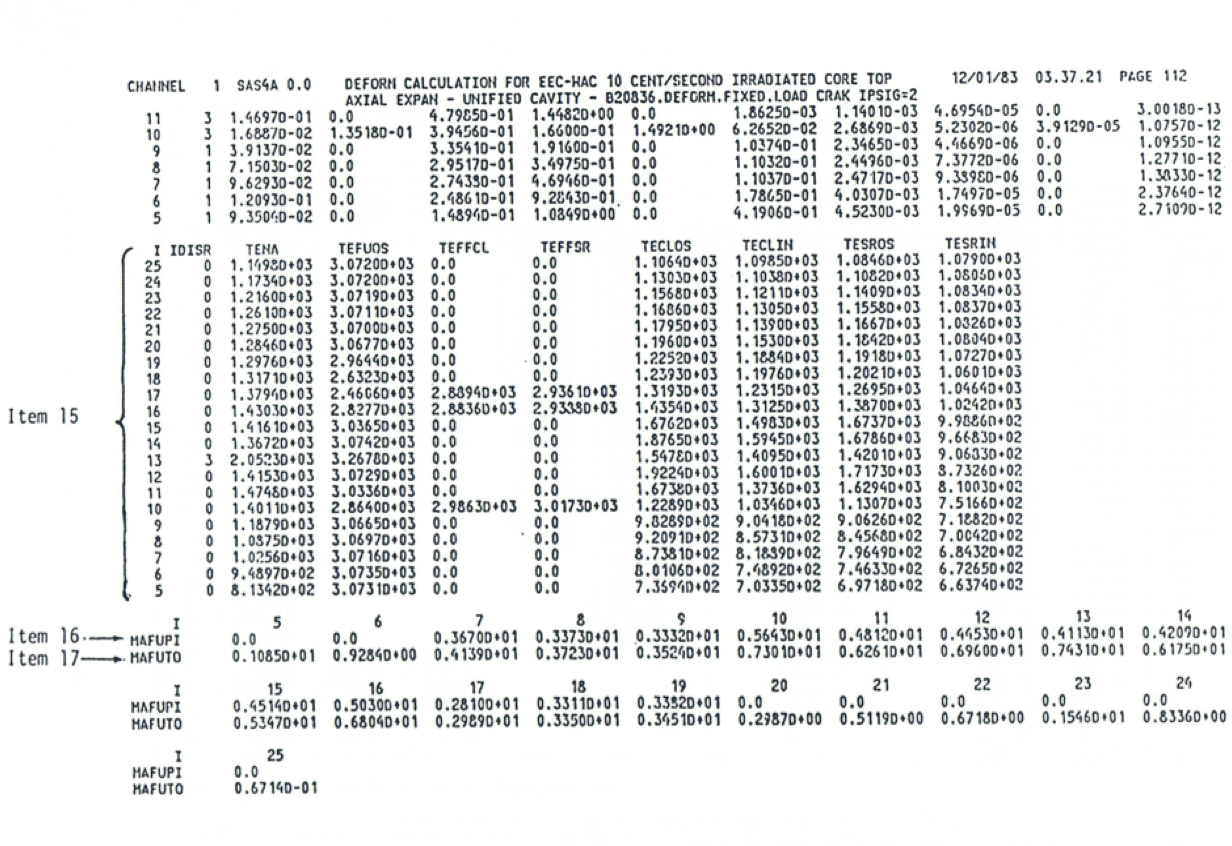
Figure 14.8.3 Sample Output from PLUTO2 Module showing the Various Items of Output Described in Section 14.8.2 (Cont’d)¶
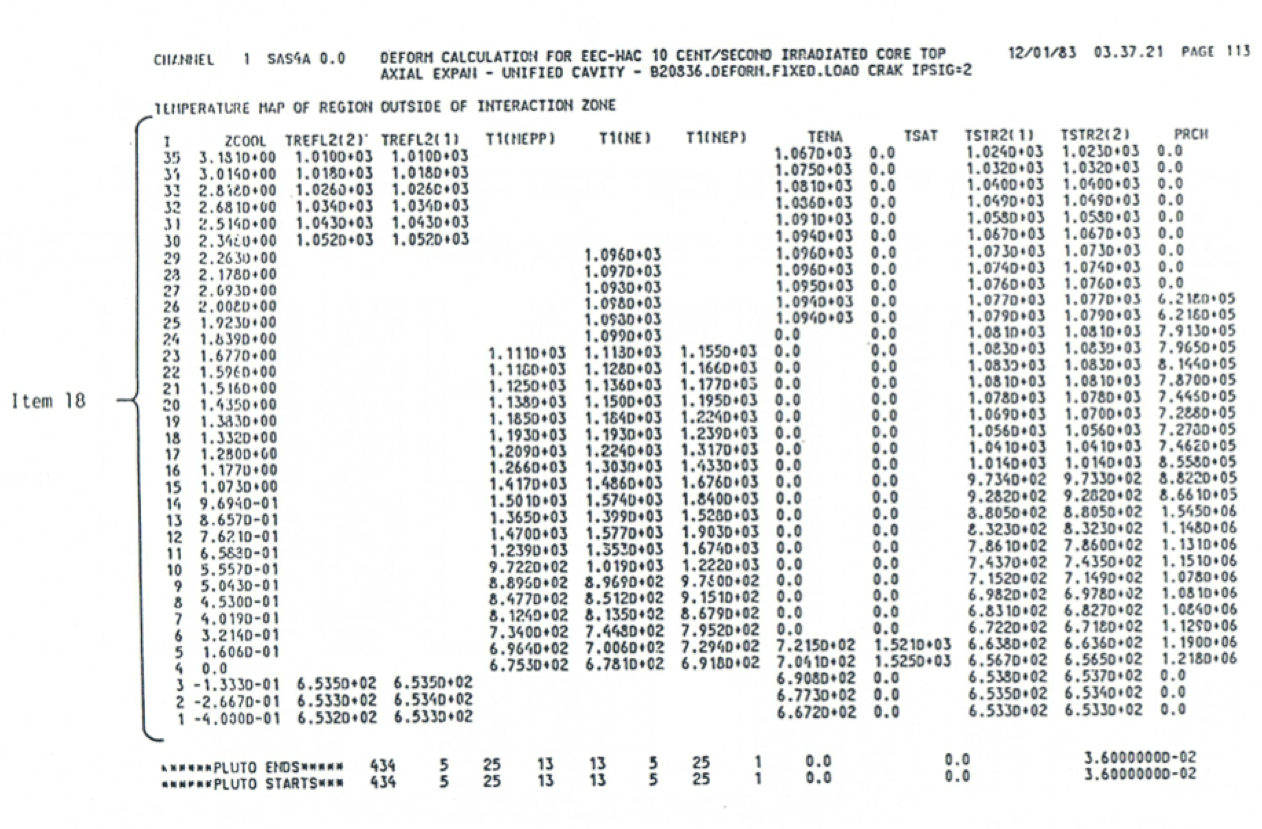
Figure 14.8.4 Sample Output from PLUTO2 Module showing the Various Items of Output Described in Section 14.8.2 (Cont’d)¶