14.7. Code Logic Description¶
14.7.1. PLUTO2 Initialization¶
For the initialization of PLUTO2, the flow diagrams in Figure 14.7.1 and 14.7-2 are relevant. The flowchart in Figure 14.7.1 shows part of the logic flow in subroutine FUINIT (FU**EL MOTION **INITIALIZATION) in which the decision is made whether PLUTO2 or LEVITATE should be initialized once subroutine FAILUR (which is called from the DEFORM Transient driver DFORM3 or from TSTHRM if cladding motion has already begun) has predicted pin failure. A minimum fuel melt fraction equal to the input parameter FMELTM must exist in the failing node before PLUTO2 or LEVITATE is allowed to be initiated. The decision which one of the two modules, PLUTO2 or LEVITATE, is to be initiated depends on the existence and size of a boiling region at the time of failure and whether the pins are predicted to fail into a voided or unvoided region of the channel. If there is no boiling region, as in a TOP accident, or if the pins fail into the liquid region of a partially voided channel, PLUTO2 will be initiated because of its capability of treating FCIs and sweepout of particulate fuel. If there is a large voided region in the channel, in which cladding motion may already have started, LEVITATE, which is designed for voided-channel fuel motion analysis, will be initiated. For the case of fuel pins failing into a multi-bubble boiling region, PLUTO2 will be initiated if the average void fraction in this region is below 70% at the time of pin failure. If the average void fraction is greater than 70%, it will be a LEVITATE case which has to be started by first initiating PLUTO2. In this case, the flag ILEPLI is set to 1. The flow diagram in Figure 14.7.2 shows that a switch to LEVITATE will be immediately made in this case, once the PLUTO2 driver routine (PLUDRV) is entered.
The flow diagram shown in Figure 14.7.2 shows how PLUTO2 and LEVITATE are actually initiated. In a PLUTO2 case, a check is first made to determine whether cladding motion has already begun. This is an unlikely situation that cold only come about if liquid sodium reentered into the boiling region after cladding motion had begun. This would have prevented the selection of LEVITATE. Since PLUTO2 cannot handle this situation, control is returned to subroutine FAILUR, and no fuel motion initiation will take place until the run has proceeded further and led to a more extensive boiling region that allows the initiation of LEVITATE.
In subroutine PLSAIN (PLUTO2 SAS4A COOLANT CHANNEL INITIALIZATION), the coolant mass, temperature and velocity distributions are initialized. In the case of a nonboiling channel, this is relatively straightforward, whereas it is quite complex to properly translate these quantities from the Lagrangian grid of a multi-bubble boiling module to the fixed Eulerian PLUTO2 grid.
In subroutine PLINPT (PLUTO2 INPUT), the coolant channel geometry is set up, all arrays relevant for the multi-component flow in the channels are initialized, and the geometry of the molten fuel cavity in the pins is established. The size of the latter depends on the radial and axial extent of fuel melting calculated by TSHTRN (for nonboiling cases) or TSHTRV (for cases in which boiling had already begun) and on the fuel-pin grid deformation calculated by DEFORM. The radially averaged internal fuel energy in the molten cavity is calculated based on the radial temperature profile in the cavity. The total fuel and dissolved fission-gas masses in all cavity nodes are also calculated. The latter are based on the DEFORM calculated values.
In subroutine PLSET (PLUTO2 SETUP), the molten cavity pressure, which is calculated by DEF”ORM and which can also be input (see input value PCFAIL) for parametric studies, is used to determine the mass of free fission gas in each cavity node. This was discussed earlier in more detail in Section 14.2.2. All other arrays necessary for the in-pin calculation are also initialized. Moreover, several channel arrays for the cladding and structure temperature calculations in the interaction region are initialized in this subroutine.
Subroutine PLSET1 (PLUTO2 SETUP1) initializes parameters necessary for the temperature calculation in the liquid coolant slugs, which is performed in subroutine PLCOOL. Moreover, parameters necessary for the temperature calculation in the structure, plenum cladding and reflectors outside the PLUTO2 interaction zone (which is performed in subroutine PLSTR) are initialized in PLSET1.
The flowchart in Figure 14.7.2 also shows that LEVITAE uses most or all of the PLUTO2 initialization routines. However, LEVITATE also needs subroutine LESAIN for the case of a single large initial boiling bubble and subroutine LECLIN if cladding motion has started prior to pin failure. It can also be seen in Figure 14.7.2 that the flag ICALC is set to 2 on the LEVITATE branch and 3 on the PLUTO2 branch. This flag controls whether the LEVITATE driver routine LEVDRV or the PLUTO2 driver routine PLUDRV will be called when the SAS4A transient driver TSTHRM is executed during the next coolant time step.
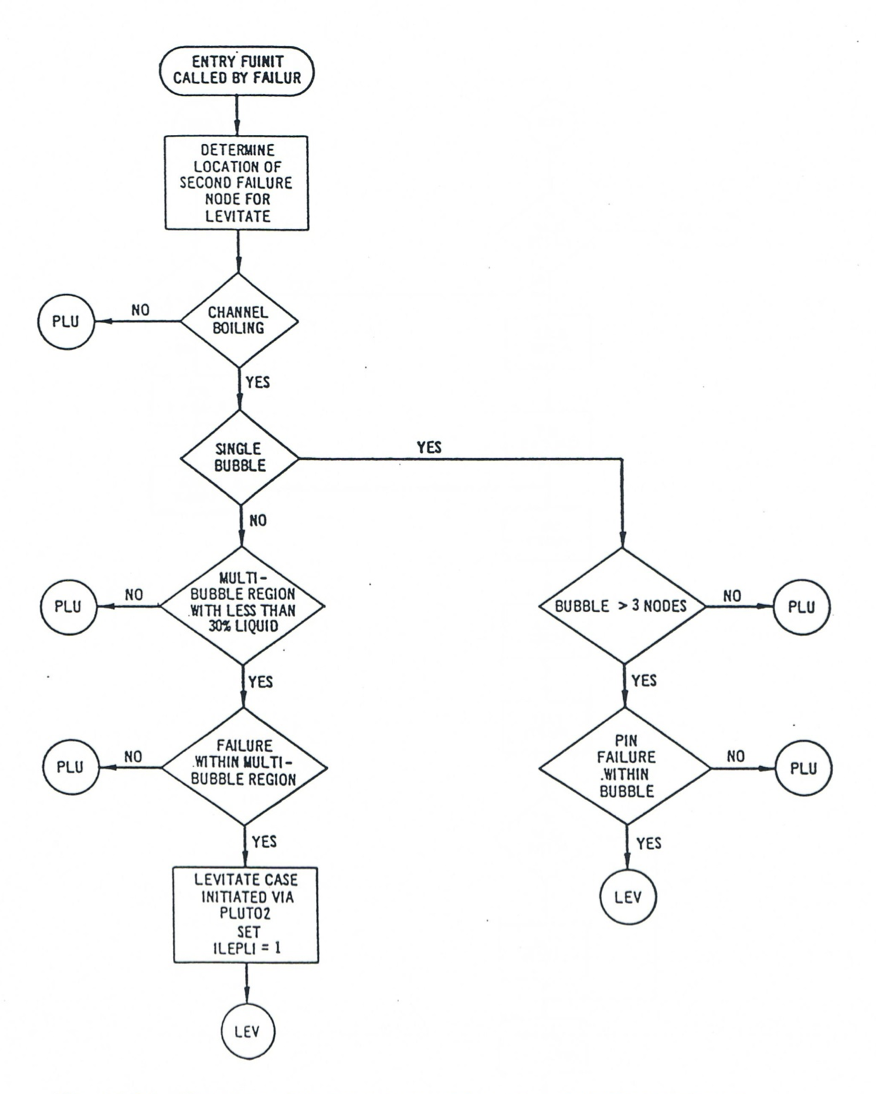
Figure 14.7.1 First Part of the Flow Chart of Subroutine FUINIT Showing the Logic Used in Determining Whether the PLUTO2 Module of the LEVITATE Module is to be Activated. The Branch PLU or LEV Implies that the PLUTO2 Module of the LEVITATE Module is Respectively Activated. The Details of Branches PLU and LEV are Shown in Figure 14.7.2.¶
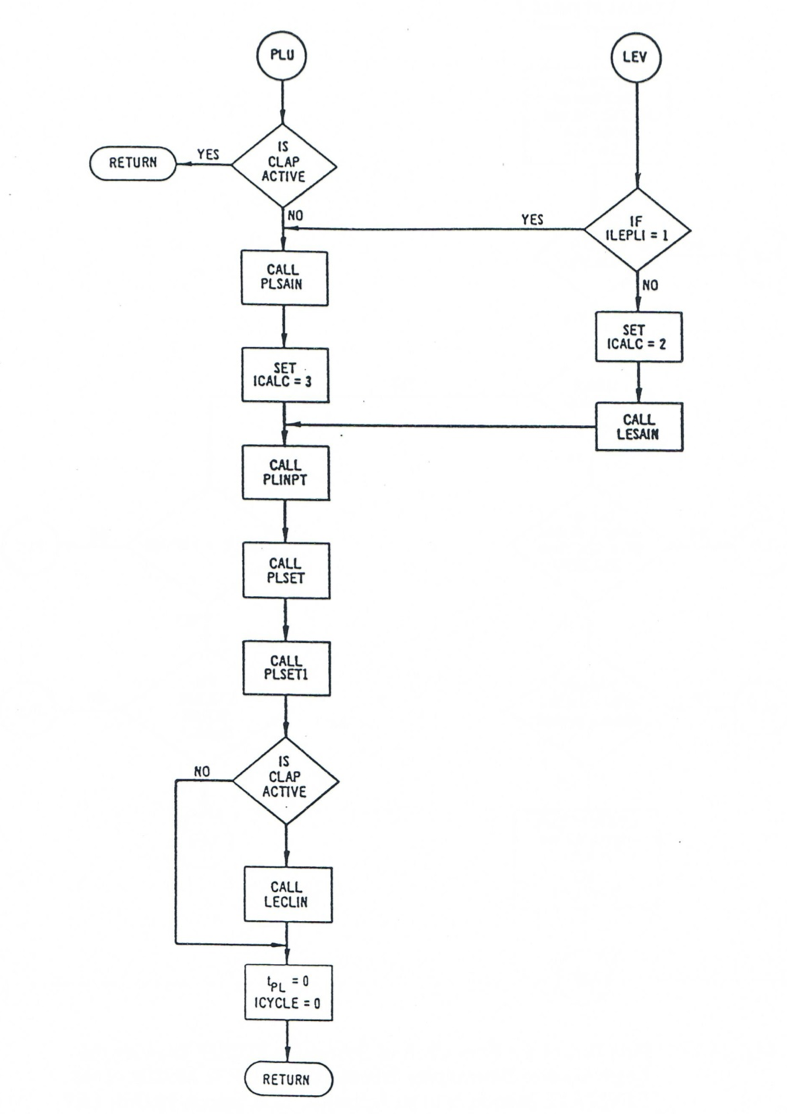
Figure 14.7.2 Second Part of the Flow Chart of Subroutine FUINIT Showing the Initialization of the PLUTO2 and LEVITATE Modules¶
14.7.2. Time Step Considerations and Auxiliary Subroutines¶
The PLUTO2 flow logic has already been described in considerable detail in Section 14.1.2. Here, only the different time steps involved and the calling of auxiliary subroutines will be discussed.
The flow diagram of the PLUTO2 driver routine PLUDRV, which already appeared in Section 14.1.2, is also shown in Figure 14.7.3 in order to have a complete set of PLUTO2 flow diagrams in this section.
The PLUTO2 driver routine can be called by the SAS4A transient driver TSTHRM at the beginning or at any time during a primary loop time step. The latter is common for all SAS4A calculational channels and is smaller than or equal to the main (point kinetics) time step, which is also common for all SAS4A channels.
Before PLUDRV is called for the first time in a given channel, the PLUTO2 time (TIMEPL), which is counted from the time of pin failure, is set to zero in the FAILUR routine. Moreover, the time of pin failure relative to the time of the accident initiation is recorded in the channel-dependent variable TMPLIN.
When PLUDRV is entered, TIMEPL is advanced by adding the PLUTO2 time step right after subroutine PLSET2 (which initializes temporary variables) has been called (see fig. 14.7-3). The very first PLUTO2 time-step size used is the input constant DTPLIN which is the initial and the minimum PLUTO2 time-step size. After the subroutines PLIPIN and PL2PIN have performed the in-pin calculation, a new time-step size for the in-pin motion is calculated as described in Section 14.2.8. Once all the subroutines calculating the channel fuel and sodium/gas dynamics have been called, a new time-step size for the in-pin motion is calculated as described in Section 14.2.8. Once all the subroutines calculating the channel fuel and sodium/gas dynamics have been called, a new time-step is calculated for the channel hydrodynamics (see Section 14.4.6.4). This is compared with the time-step size calculated for the in-pin motion and the smaller of the two will be used as the new PLUTO2 time-step size if it is larger than the above-mentioned input value DTPLIN. If it is smaller than DTPLIN, the latter will be used as the new PLUTO2 time-step size. Also, if it is larger than \(2 \times 10^{-4}\) s, it will be set to this value. Moreover, if the newly determined time step extends beyond the end of a heat-transfer time step, it will be cut back such that the new PLUTO2 time will coincide with the end of the heat-transfer time step. This is possible since the heat-transfer subroutine PLHTR calculates only the fuel temperatures in the region determined by the interaction region (see Figure 14.1.4 in Section 14.1) and the fuel and cladding temperatures outside the interaction region. None of these temperatures are changing rapidly relative to PLUTO2 time-step sizes.
The determination of the heat-transfer time step is made using a series of tests. First, the initial and maximum heat-transfer time step is set to 1 ms, which is about an order of magnitude smaller than the characteristic heat-transfer time for cladding. If the initial or any later time step is larger than the current primary loop time step, it is set equal to the latter. Since the primary loop time step has to be less than or equal to the main (point kinetics) time step, it is, of course, also limited by the main time step.
The heat-transfer time step is not only used for the heat-transfer calculation of all the fuel and the cladding reflector, and the structure temperature calculation outside the interaction region, but also for the temperature calculation in the liquid sodium slugs. Since the latter involves not only heat conduction from the walls but also heat convection from the coolant cells above and below the one considered, the heat-transfer time step is also limited by a Courant condition based on the liquid slug velocity.
The flow diagram in Figure 14.7.3 shows that PLUTO2 retains control and advances the solution using PLUTO2 time steps until the end of the primary loop time step is reached. This is different from the single-phase hydraulics driver TSCL0 and the boiling module driver TSBOIL, which return control to the SAS4A transient driver TSTHRM after every coolant time step. The latter is the basic time step in the modules controlled by TSCL0 and TSBOIL. In PLUTO2 (and LEVITATE) the coolant time step is set equal to the primary loop time step. PLUTO2 or LEVITATE thus also return control to the transient SAS4A driver at the end of this “artificial” coolant time step.
Several auxiliary subroutines used in the PLUTO2 module are not shown in the flow chart in Figure 14.7.3. These include the function subroutine TEFUES, which calculates fuel temperatures for a given internal fuel energy and TESEEG which calculates steel temperatures for a given internal steel energy. Function subroutines EGFUTE and EGSETE perform the inverse operation for fuel and steel, respectively, i.e., calculating internal energies for a given temperature.
Several auxiliary subroutines and subroutine functions are called by the subroutine PLHTR performing the heat-transfer calculation in the solid annulus of the fuel pin and in the cladding outside the interaction region. PLHTR is a derivative of subroutine TSHTN3 described in more detail in Section 3.3.1 of Chapter 3. The most important auxiliary subroutine called by PLHTR is INVRT3, which inverts a tri-diagonal matrix. Subroutines KFUEL and KCLAD calculate the fuel and cladding conductivity, respectively. Subroutine CFUEL calculates the heat capacity of the fuel and TSHTN5 corrects fuel and cladding temperatures for the heat of fusion, if melting is occurring. Subroutine HBSMPL and function subroutine HBFND calculate the gap conductance.
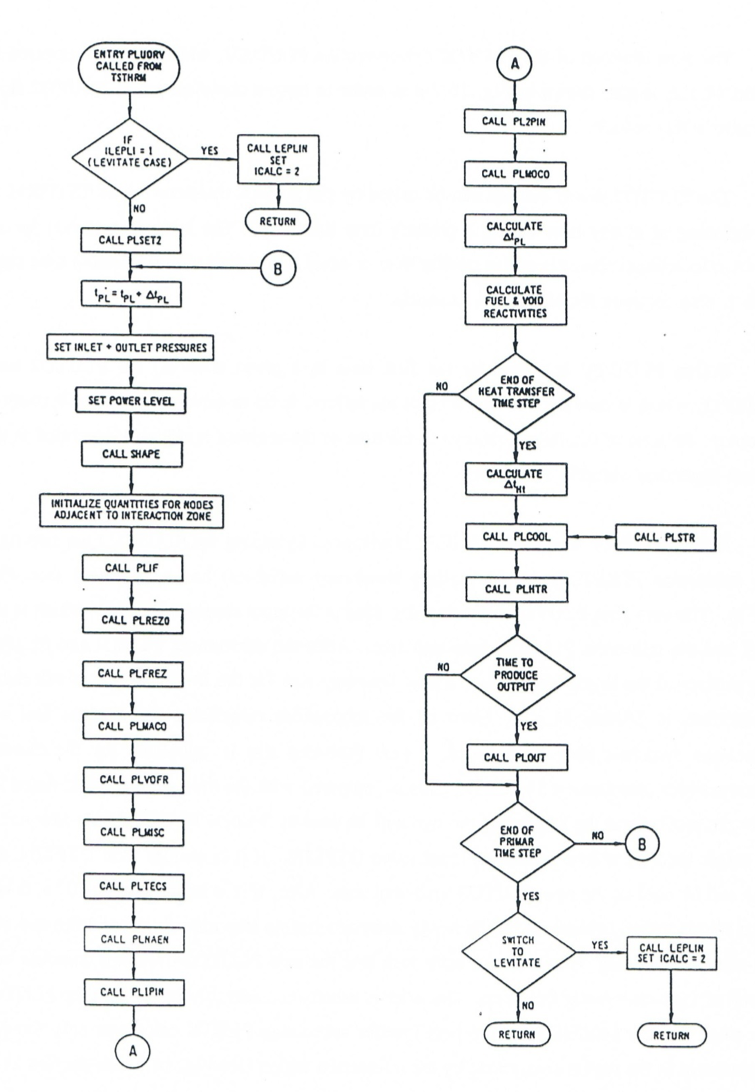
Figure 14.7.3 Flow Chart of the PLUTO2 Driver Sub routine PLUDRV¶