9.1. Introduction¶
In Version 5.7, a new metallic fuel performance model for pre-transient and transient analysis has been introduced. The new fuel model is described in the remaining sections of this chapter, the description of DEFORM-5, which is considered deprecated, has been moved to Section 9.8.8.
The integrated metallic fuel performance model accounts for the coupled nature of the uranium plutonium zirconium metallic fuel phenomena and its impact/evolution on/during safety analysis. Given the user-provided operating history, initial geometry, fresh fuel composition, mass, cladding type, and the calculated fuel pin and coolant temperature distribution, MFUEL, the metallic fuel performance model, simulates the fuel and cladding behavior as a function of time. The main capabilities of MFUEL are prediction of: 1) Fuel pin mechanics, and compositional and dimensional changes; 2) Clad failure; and 3) Fuel pin thermal resistance. Achieving these high-level goals accurately is strongly related to the model performance of individual physical processes taking place within the fuel pin during operation. Metal fuels typically operate above half of their solidus temperatures during normal as well as off-normal conditions. Availability of thermal activation provides the driving force for various diffusional processes leading to complex phase transformations, micro-structure evolution, significant amount of fuel swelling, interconnected porosity formation, excessive amounts of fission gas release, and fuel clad chemical interactions. Clad failure in fast reactors primarily occurs as a result of creep rupture augmented by clad wastage formation. The reaction is driven by thermal creep induced dislocation motion, grain boundary cavity nucleation, and growth and breakup of grain boundaries. The high-level complexity and limited available data requires introducing physics-based modeling approaches to gain extrapolation ability and sensitivity with respect to various conditions.
As shown in Figure 9.1.1, the MFUEL driver evaluates the different physical phenomena, described in Section 9.2 at each time step. At the end of each time step, the MFUEL driver updates the fuel pin geometry, fuel pin composition, plenum pressure, fuel porosity, bond sodium infiltration, and clad failure margin. Each of these quantities has an impact on the fuel pin thermal-hydraulics, reactivity feedback, and margin to fuel melting.
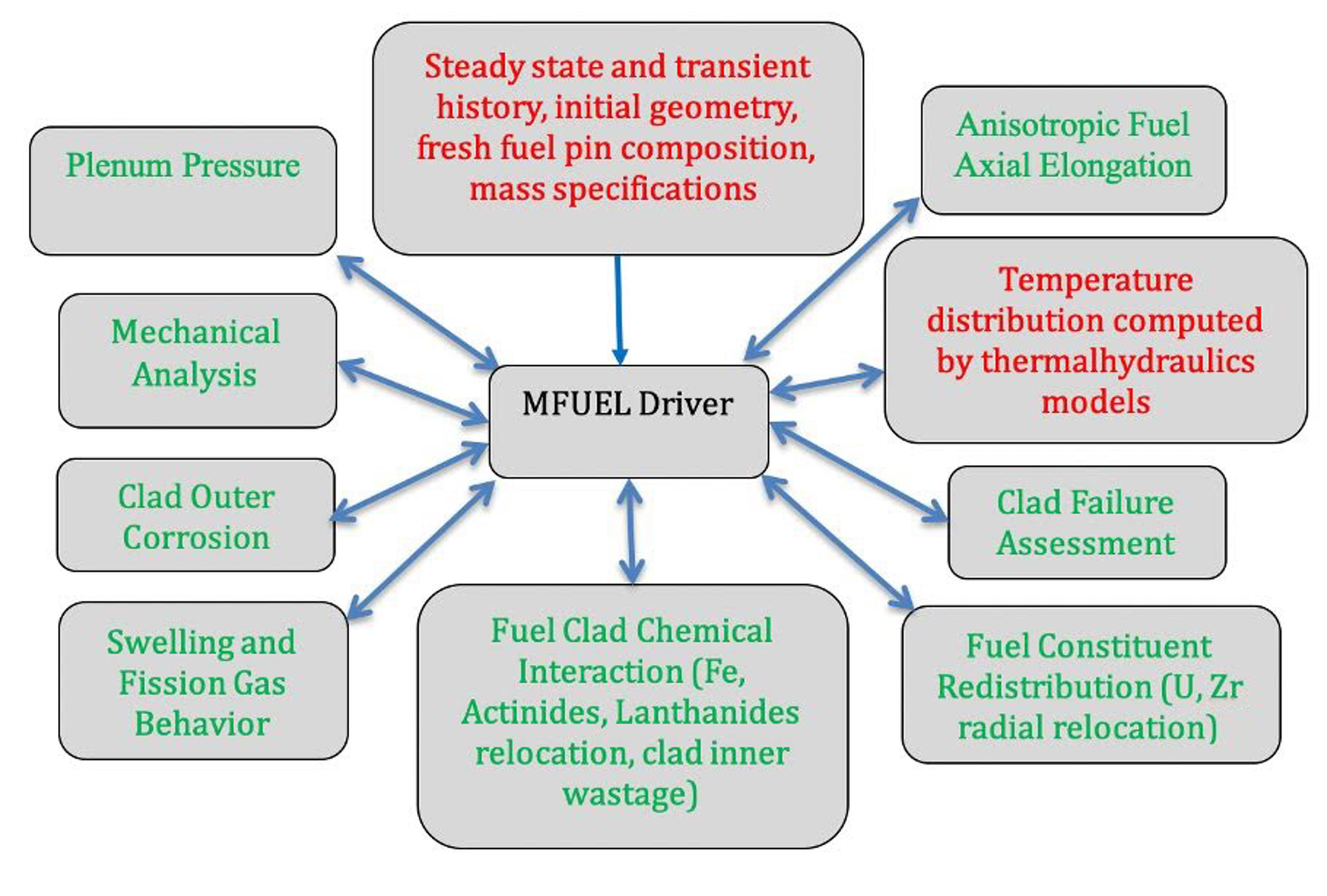
Figure 9.1.1 MFUEL - Integrated Metal Fuel Models. Processes shown in red are handled by other SAS models and processes shown in green are handled by the MFUEL driver.¶