12.2. Liquid Slug Flow Rates
The mass flow rate in each of the individual slugs pictured in Figure 12.1.1 is computed from the momentum equation similarly to the calculation of the prevoiding mass flow rate described in Chapter 3. Because of this similarity, the discussion here will be brief and will emphasize the additions that must be made to the model of Chapter 3 to accommodate the fact that there are several separate liquid slugs in the channel rather than one slug which fills the channel as in the prevoiding case. In particular, the model must now be able to handle the fact that the liquid slugs are continually changing length and must account properly for the effect of the bubble vapor pressures in driving the liquid slug flow rates.
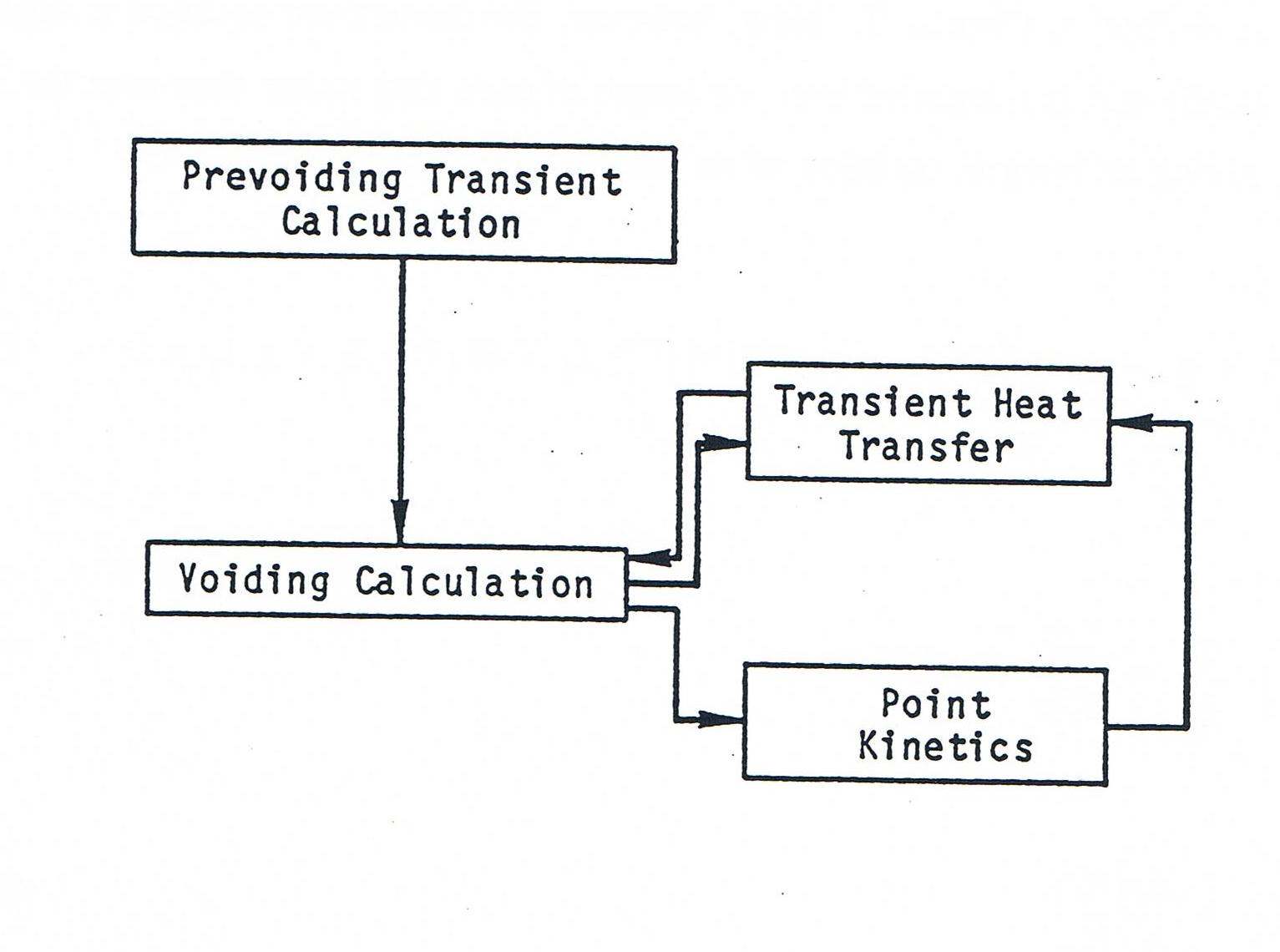
Figure 12.2.1 Schematic Drawing of the Relationship of the Voiding Model to Other SASSYS-1 Models
The foundation of the model is again the liquid momentum equation, Eq. (3.9-1):
with the terms as defined in Chapter 3. Now, however, the momentum equation is applied to each slug individually and is integrated over the length of each slug rather than over the length of the channel, giving an integral equation of the form of Eq. (3.9-8):
where
where
Pb= the pressure at the bottom of the slug,
and
Pt= the pressure at the top of the slug.
The variable JST is the number of the mesh segment in which the bottom of the liquid slug is located, while JEND is the number of the segment in which the top is contained. The liquid slug configuration in the SASSYS-1 axial mesh is shown in Figure 12.2.1. Note that mesh segments JST and JEND are part liquid and part vapor. Since the integration is over only the liquid portions of these segments, the axial length terms Δz(JC) in the expressions for XI1, XI3 and XI5 must be altered for segments JST and AJEND from being the mesh segment height to being the length of the portion of the segment which is filled with liquid. This is represented by the term Δz′
The notation zi(L,t,K) for the interface position is derived from the coding and is to be interpreted as follows. The quantity L takes the value 1 or 2, with L=1 denoting the lower interface of bubble K and L=1 the upper interface. The variable t is simply time, and K is just the bubble number, with the numbering going from 1 for the lowest bubble in the channel to Kvn for the highest bubble.
Two other modifications must be made to accommodate the partial segments at the ends of the slug. First, the density pc(JST) in the expressions for XI2(JST) and XI3(JST) must be replaced by the liquid density at the bubble interface; similarly, ρc(JEND+1) must be replaced by the interface value in XI2(JEND) and XI3(JEND). Second, the terms for JST and JEND in the computation of I4 must be multiplied by the fraction Δz′/Δz.
If JST = 1, the effective inertial term [ΔziA]b must be added to I1, and if JEND = MZC, the term [ΔziA]t must be included in I1, just as in Chapter 3, Eq. (3.9-9).
In the special case of a small liquid slug entirely contained within one mesh segment, JST = JEND. Then,
and there is only one term in each of the summations for I1 through I5.
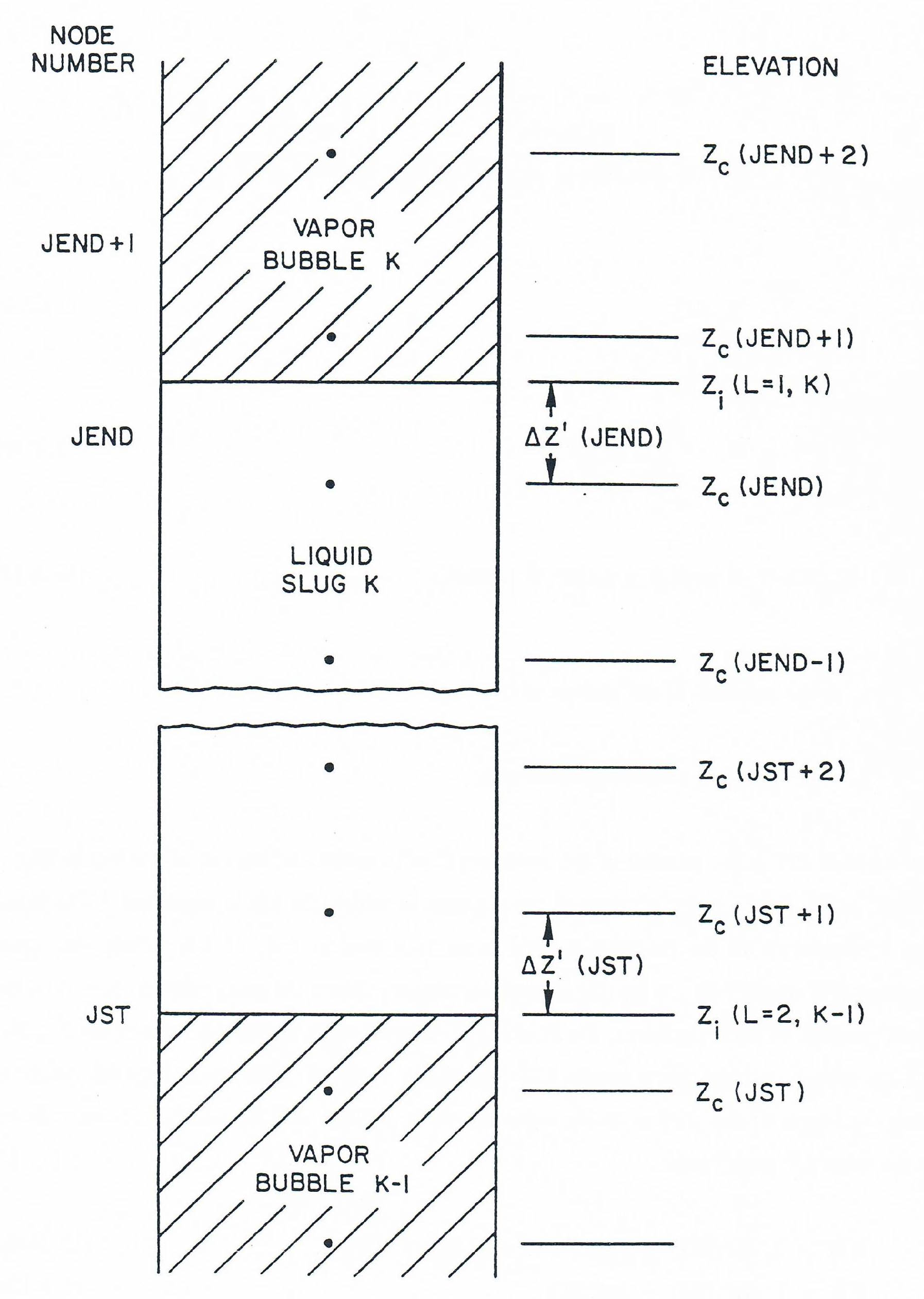
Figure 12.2.2 Placement of a Liquid Slug in the SASSYS-1 Axial Coolant Mesh
Eq. (12.2-2) must now be finite differenced and solved for the liquid mass flow rate in the slug. The advanced time mass flow rate W is forward differenced in time, and functions of W in Eq. (12.2-2) are expressed using first-order Taylor series; see Eq. (3.9-26) through Eq. (3.9-33) for the detailed expressions. However, the differenced form of Eq. (12.2-2) is more complex than the corresponding equation in the prevoiding model, Eq. (3.9-35), because now the coefficients I1 through I5 are functions of time due to motion of the liquid-vapor interfaces, and, therefore, the time level at which these coefficients are evaluated must be specified. To allow flexibility in the level of implicitness of the calculation, the variable explicit/implicit scheme used in Eq. (3.9-26) is applied to the coefficients in Eq. (12.2-2). The differenced equation is then
The change in the coefficient I2 over a time step is a function only of the change in interface liquid density, which is a very small effect and can be neglected. Therefore, I2 is considered constant over the time step. In addition, the orifice coefficient I4 is also assumed constant over the time step. The advanced time values of the other three coefficients are expressed using forward differencing in time. To illustrate, take the gravity coefficient I5; at time t,
and at time t+Δt,
These two integrals are identical except in segments JST and JEND, where the bubble interface positions are changing with time. Taking the difference gives
The interface position zi can be written as a linear function of the interface velocity vi, so that
Therefore, I5(t+Δt) is
If the velocity is assumed to vary linearly over the time step, the time integrals in Eq. (12.2-22) become
where Δv=vi(t+Δt)−vi(t). Therefore, I5(t+Δt) is
This expression is valid for a liquid slug that is bounded at both ends by vapor bubbles. However, slugs that extend out the top of the subassembly do not have a moving upper interface, and so the integral over the upper interface in Eq. (12.2-20) is zero. Similarly, the integral over the lower interface is zero for slugs extending out the bottom of the subassembly. To preserve the ease of using one expression for I5(t+Δt) for all types of liquid slugs, Eq. (12.2-24) is rewritten as
where
Slug type 1 refers to a slug that extends below the subassembly inlet, type 2 to a slug that is bounded top and bottom by bubbles, and type 3 to a slug that extends out the subassembly Table 12.2.1 defines all slug-type numbers used in the code, as well as listing the bubble-type numbers that are part of the coding. Note that the increment ΔI5 represents the change I5 if the change in the mass flow rate of the slug is ignored, while the I′5 term accounts for the change due to acceleration of the slug.
The expressions for I1(t+Δt) and I3(t+Δt) are derived in the same way as was Eq. (12.2-25). The resulting equations are
where
with
and
The effect of slug acceleration is omitted in I1(t+Δt).
|
|
The FORTRAN variable IBUB1 and IBUB2 refer to bubble types. |
|
IBUB |
Bubble Type |
1 |
Bubble within the subassembly; uniform vapor pressure bubble. |
2 |
Bubble within the subassembly; pressure gradient model. |
3 |
Bubble extends out the top of the subassembly; uniform vapor pressure bubble. |
4 |
Bubble extends out the top of the subassembly; pressure gradient model. |
5 |
Bubble extends out both the top and bottom of the subassembly. |
6 |
Bubble extends out the bottom of the subassembly. |
|
|
The FORTRAN variables ILIQ1 and ILIQ2 refer to liquid slug type. |
|
ILIQ |
Liquid Slug Type |
1 |
Lower liquid slug, below the lowest bubble. |
2 |
Intermediate liquid slug, with bubbles above and below. |
3 |
Upper liquid slug, above the highest bubble. |
4 |
Liquid slug fills whole subassembly; no voiding. |
5 |
Lower liquid slug below the subassembly inlet, below a type-5 or -6 bubble. |
6 |
Upper liquid slug above the subassembly outlet, above a type-3, -4, or -5 bubble. |
Substituting the above expressions for the advanced time coefficients into Eq. (12.2-17) and neglecting second-order terms produces the differenced momentum equation
which gives
where
and
Thus the change in flow rate for a liquid slug is related to the changes in vapor pressures in the bubbles above and below the liquid slug, or to the changes in inlet and outlet coolant pressures.